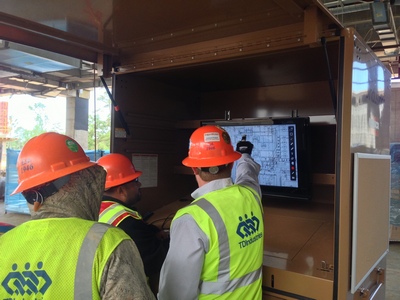
By Payton Hill & Jason Hart
From digital planrooms to LiDAR scanning and tablet computers in the field, the construction industry is embracing new technologies that save time and money for their clients and deliver instant and accurate communications across project teams and jobsite personnel. General and specialty contractors and engineering firms agree that the benefits of utilizing new tools for early clash detection and to implement design and owner-driven changes are compelling reasons to invest and deploy these technologies across a wide range of projects, including airports, corporate facilities, hospitals, industrial plants and sports stadiums, among others.
Peyton Hill, project superintendent for specialty contractor TDIndustries, explains, “We utilize Plan Grid which is a PDF-based storage application. All of our foremen and superintendents have iPads with this app on them. We can load blueprints, specifications and shop drawings, including requests for information, enabling everyone on the jobsite to have immediate access to the job. If we receive a change order or new set of drawings, we load those up via the web, and the system notifies everyone on the job about these changes instantaneously. In the past, with paper-based blueprints, we had to gather all of the old ones, replace them with updated blueprints and verify that all of our field and home office personnel were working from the same, updated documents. That was very time-consuming.”
Adds Hill, “Communications on the jobsite can often be the biggest challenge. With Plan Grid, we can post changes and all project personnel, whether at the home office or on the jobsite, will have the same information.” For bilingual communications, TDIndustries provides a toolbox application that addresses important topics, such as safety, in both Spanish and English. A translation app is also available for use.
Engineering firm JQ employs tablet computers to save time documenting the firm’s field work and to have project information available to their teams of structural, civil and survey engineers while onsite. According to JQ Principal Jason Hart, P.E., LEED AP, who oversees the company’s power and industrial projects, “By having project documents available onsite, we can resolve issues faster. A quick brainstorming session with the designer and the contractor can also be more productive than an endless stream of emails going back and forth among the project team.”
For project conflict detection and coordination in the design phase, JQ has invested in LiDAR mapping equipment, a remote sensing technology that measures distance by illuminating a target with a laser and analyzing the reflected light.
According to Hart, “Healthcare, higher education and corporate facilities are markets where LiDAR can be a differentiator when comparing construction companies. Facility managers and operators involved in the selection process often look beyond the end of construction to new methods of fast-tracking projects and saving on construction costs. They want more than the BIM model from the designer. They want to know where the pipes, conduits and other components are in their building, and a reliable, as-built model based on laser scan data that includes this type of detail can create loyal customers.”
Quality assurance is another benefit of utilizing new technologies, according to Hill who is working on a multi-year project for Exxon Mobil. “The owner does his own inspections onsite and expects us to be there with current information. Plan Grid enables us to pull up the specifications and answer any questions that might arise.”
”We also employ Trello, another application that assists with project activity tracking. It is a simple-to-use app that allows the project team to communicate and track their progress instantaneously. One way in particular that we utilize Trello is to track our BIM-coordinated shop drawings. Through Trello, the team members can easily update their drawing schedules and review approval status. Since all team members” updates are visible, the team members can check status without having to send emails or make follow-up phone calls. In this way, Trello has helped to streamline our flow of information within our teams.”
From motivating a team to fast-tracking a project, to ensuring accuracy and quality on the job, new technologies are driving changes in the construction industry that will become best practices now and into the future.
JQ’s Jason Hart sees an evolution of facilities information modeling that will be led by construction companies and large mechanical contractors positioned to establish and maintain FIM systems for clients. “FIM is an exciting area, held back by software incompatibility and lack of industry standards at present, but FIM will become an important, additional service that continues beyond the construction of a facility,” says Hart.
Hill believes project teams that embrace innovation and new technologies will influence others to do the same.
“By using these technologies with owners and developers, other project teams will be pushed to deploy them. Our younger workforce expects them, too, because they already use them in their daily lives. They see the benefits of innovation, especially in the construction industry.”
Peyton Hill, a senior superintendent for TDIndustries, has been in the HVAC mechanical and plumbing construction industry for 25 years. His experience includes residential, commercial and industrial projects in multiple sectors. Hill may be reached at Peyton.Hill@TDIndustries.com. Principal Jason Hart, P.E., leads the Industrial Facilities group at JQ. The group works with industrial and power companies to design structures for plant capital improvements, renovations and maintenance. LiDAR and BIM are frequently used in these projects. Hart may be reached at jhart@jqeng.com.