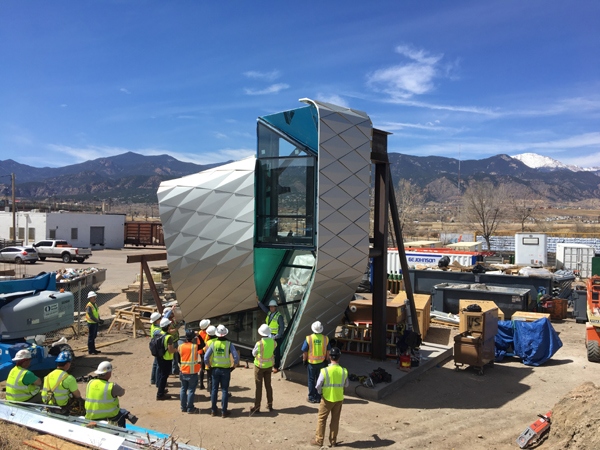
By Sean O’Keefe
Leaving a legacy often requires a lifelong fortitude of purpose and character that only the best among us can realize regardless of pursuit. In athletics, the pinnacle of success is that of an Olympic gold medalist, a champion among mankind. In construction and design, legacies may not be as easily quantified but once the truly spectacular is achieved it’s hard to overlook. When the new United States Olympic Museum in Colorado Springs, Colorado opens to the public, it will add to the legacies of design architects Diller Scofidio + Renfro and general contractor/construction manager GE Johnson Construction Company.
“The incredible architecture we are delivering is challenging all of us to think beyond boundaries,” says GE Johnson Superintendent Tim Redfern. Redfern and GE Johnson Construction’s team are tasked with assembling a structure unlike any other ever built.
DS+R’s design for the museum takes its athletes as inspiration; the design idealizes athletic motion by organizing its programs – galleries, auditorium and administrative spaces – twisting and stretching centrifugally around an atrium space. Arriving at ground level, visitors are whisked to the top of the building via elevator where they are greeted by a grand view of snow-capped Pikes Peak, an ode to Olympus with its own majestic presence. Circulation unfurls organically, gradually spiraling down through the museum’s series of loft galleries at a pace propelled only by the individual’s own inquisitive nature and gravity. The folded planes of the building’s superstructure create helical volumes of space circling the introspective atrium. Dissected by the structure and connected by a continual downward ramp, perched floor plains filled with interactive galleries will memorialize the accomplishments of U.S. Olympians past, present and future.
“The dynamic building form defies typical construction. Thinking outside of the box is not an adequate description of what we’re doing to make this happen,” shares Redfern.
The design’s diverse elevations called for 15 independent concrete slab-on-metal deck elevations, scaling just four stories of construction with no two planes running parallel for long. Structural tolerances are ultra-tight, becoming even less forgiving as the structure goes up – the opposite of most builds. The exterior frame tolerance is two inches, while interior frame tolerances are only a quarter of an inch, with just an eighth of an inch of deflection. Controlling precise placement of every piece of an intricate puzzle like the United States Olympic Museum is a process that can only be accomplished through what the general contractor thinks of as a spirit of continuous improvement.
GE Johnson is pre-thinking and rethinking every move by incorporating a 3D point cloud that provides an accurate digital record of physically intangible space. All subcontractors are required to use the point cloud to develop approvable shop drawings. The point cloud is integrated with the BIM model, which draws from several computer-aided design, graphics, engineering and manufacturing programs, along with the discipline-specific platforms of a variety of different subcontractors. Integrated work plans developed with subcontractors define every aspect of each construction activity including who, what, when and where. Most importantly, plans will detail how each piece is assembled, verified and validated for accuracy against the overall model as tasks complete. Looking beyond typical clash detection, the contractor’s fully detailed steel fabrication model allows the clearances of each structural framing member to be independently checked to make sure the design’s distinctive shell of diverging planes and scaled metal skin reads as intended.
The museum’s unique exterior skin aptly illustrates the intricate precision of purpose and combination of expertise required to succeed at the Olympic level. The façade will be covered in more than 9,000 individual diamond-shaped anodized aluminum petals that interlock to form a single, beveled surface with integrated drainage channels. In total, an estimated 27,000 anchor points will attach the exterior wall sections to the structural frame. The specific details of every panel from backing materials, sheathing and waterproofing will all be independently analyzed within the model because seemingly every petal is either uniquely shaped, placed or attached. The contractor brought highly specialized subcontractors who had previous experience with similar configurations onto the team to achieve the use of these unusual building materials and intricate assembly processes.
Even as the structure reaches its highest elevation, preconstruction activities continue. For the specialized subcontractors developing a sequence of efficiently attaching the exterior skin to the structure, nothing is more valuable than the full-scale exterior wall section being erected onsite. It’s estimated that the 20-foot-by-20-foot mock-up wall section will require more than 1,000 labor hours to assemble and will likely cost in excess of $150K to build. Eight different subcontractors must delicately interlace their work through a maze of structural framing, light-gauge framing, waterproofing, drainage, glazing and aluminum panels. Identifying components within wall sections that can be prefabricated offsite, like the micro-framing system and laser cutting framing plates, increases quality control and supports repeatable processes during construction. Each component is individually numbered indicating where, how and to what it attaches like a giant model and each placement can be checked against the point cloud to verify accurate alignment.
Thinking outside of the box hasn’t been limited to solving challenges on the outside of the building. Placing the museum’s extremely large, yet whisper quiet, air handling unit has presented a series of sequencing challenges with a ripple effect that will likely continue to reverberate.
“It’s low-speed, high-volume and is by far the largest air handler I’ve ever put in,” says Redfern enthusiastically. “The size dictates a basement placement, which meant installing it before we put in the structural steel for level one.” Once installed, this unorthodox situation left the massive (and expensive) unit unprotected from the weather until the floor above it could be dried in. Complicating matters, structural engineering indicated that the concrete floor slabs across the building’s many elevations should be poured from the top down to deflect loading. Waiting until the museum’s 15 elevations were poured and cured would greatly extend the exposure period for the mechanical system, presenting significant risk and an extremely difficult situation to rework if the unit was damaged. ‘’We encouraged the owner and design team to install terrazzo on the first level floors in lieu of stained concrete so that floor placement could be moved up in the schedule, increasing protection of the AHU and equipment below.”
Placing the air handling unit first also required fireproofing the basement before setting structural steel, one of several conditions, which make multiple mobilizations of key trades likely throughout construction.
“We have been empowered to use ingenuity to solve complex challenges at every turn on a very, very cool building,” says Redfern. “GE Johnson is using anything and everything we can to build this right. Pushing boundaries, gaining outside expertise, and asking more of oneself than others will is the Olympic spirit this museum is being built to honor.”
Sean O’Keefe Communications and Strategy provides marketing and public relations services to the design, construction and commercial building products industry.