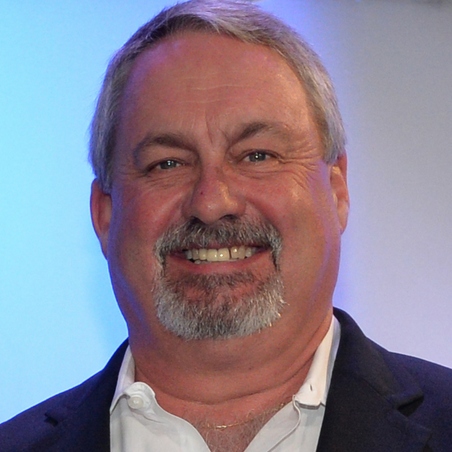
Construction challenges, industry changes & must-have tech tool
By Chris Maday Schmidt
Tony Creed, senior superintendent at TDIndustries, began his career as a sheet metal helper. Through hard work and determination, he has become the company’s leading superintendent for data center projects. One of Creed’s major commitments has been Lean initiatives. He has seen the industry change to incorporate these processes, but has also seen what happens when a project development team does not have complete buy-in from all partners. Join Construction Superintendent as Creed offers words of wisdom to his younger self and to aspiring superintendents, the biggest change he’s witnessed in the industry over the past four decades, his insights on the labor shortage and more.
(Q) How do you engage project team buy-in as far as Lean initiatives?
We have a core group that has been together for almost four years. It has really helped to set an example for new partners. Lean is part of every action on our jobsites, so everyone needs to be involved.
Communication is also important. New partners’ observations, in some cases, are more important than a superintendent’s, because they are actively working in the frontlines. We make it very clear up front that one of our tools for success is Lean. If they’re not familiar with it, we show and support them to get them up to speed.
(Q) What advice would you give your younger self just starting out in the industry?
Today’s generation is so proficient with technology. I would never have dreamed we would be so dependent on it. Their skills are crucial, but don’t think just because you can fix a flickering tablet you know everything about construction. Listen to experienced partners, and don’t be afraid to ask questions.
Also, I’d tell myself to focus on the future, not your past. You are responsible for your growth. Supervisors will see your initiative and help you improve.
(Q) Speak to some of the unique challenges of constructing mission critical projects, such as data centers.
If you take all the data created since the dawn of man, 90 percent of it has come in the past two years. That’s not slowing down anytime soon, and data center companies are feeling pressure to finish faster to keep up with demand. Sometimes schedule change orders are simply undeliverable due to site restrictions or manpower requirements. We’re always willing to work with our customers to find the best possible solution, but changes are not always possible.
(Q) What are the significant changes you have seen throughout the years in data center construction?
All data centers used to be on raised floors and in small, self-contained rooms. Now, we’re talking about huge, built-up systems on data floors, sometimes 1 million square feet. There’s a lot more to think about in a big room: cooling, airflow, safety, energy delivery and spacing, just to name a few. Today, system shutdowns have to be carefully managed, and extra fail safes must be considered.
(Q) Any insight on what you feel may help with the skilled worker shortage?
There are many reasons for our current cultural aversion to the skilled trades, but one thing we can all do is introduce them as career paths before kids’ preconceptions are hardened. Most companies will lump this in with recruiting, and focus on high schools where their return is likely better and quicker. I think that’s a mistake. We need to start introducing the idea of skilled trades careers even earlier.
It’s also important to convince parents that a skilled trades career is an option. There’s good money in the trades now. Safety is emphasized in a way it wasn’t 40 years ago, and you don’t have to shell out $100,000 in student loans to pay for it. Besides, some people don’t enjoy the 9-5 grind in front of a computer for half of their life. They need to know there’s another option for them.
(Q) Talk about the most challenging project you’ve managed. How did you overcome the challenges?
I did a vertical expansion at a hospital once. It was extraordinarily complex. Working with doctors, charge nurses, the hospital board and other contractors, we had the added concern of working around systems that were essential to injured and sick patients’ recovery. We spent several weeks creating a specialized plan to avoid unnecessary shutdowns. We planned well, but there were still plenty of nerves during the scheduled shutdowns. It was a major challenge, but I’m proud we were able to communicate well and solve that problem.
(Q) Are you involved in any type of mentoring program with TDIndustries? If yes, share a bit about your role.
Every day is a chance to mentor partners. Beyond those daily lessons, I lead piping foreman meetings and help with Last Planner, Pull-Planning and piping classes. It’s a team effort to help everyone improve. We’re all involved to some degree in the success of our partners’ futures.
(Q) What words of wisdom would you offer to aspiring superintendents?
The construction industry is competitive, and a great way to differentiate yourself is to learn new tech processes. They’re not going away, and will probably be more specialized as time goes on. Lean is one of those essential tools. Encourage others to adopt the Lean way of thinking, especially general contractors, and everyone will benefit.
On your own team, make sure to listen to everyone. Learn partners’ names and who they are. People are naturally more responsive when they have a personal connection to you. You’ll see fewer employees leave and take their experience with them, too.
(Q) What is the biggest change you’ve seen in the industry since you began your career with TD in 1978?
Safety. Thank God it is a priority now. When I started, the industry, as a whole, viewed serious injuries as an unfortunate reality. Today, our goal is Zero Harm. We provide leading-edge personal protection equipment and training. We’re holding everyone from pipefitter helpers to the project manager responsible for the safety of everyone onsite, and we’ve developed offsite production methods to reduce exposure.
The biggest improvement, in my mind, is empowering all partners to take responsibility for themselves and others – even employees of other companies. Your life shouldn’t be at risk because you’re the new guy or work for another company. If you don’t feel comfortable with your safety, say something, and definitely speak up if you see someone else acting unsafely. That person may not have the same training you do.
(Q) Which tech tool is a “must have” for you on the job? Why?
It’s a given that everyone has a cell phone. Tablets, with BIM software loaded on it, are also essential. All your tools are right there. The ability to communicate immediately onsite saves so many man hours, I don’t know how a contractor could be competitive without it.
When I started, we had to take a Polaroid of an issue – or draw it by hand – then walk to the nearest phone or to the office to explain. That could take an hour. On a tight-schedule project like a data center, that’s a critical hour of work gone for good.
(Q) What is a favorite hobby you engage in when off the clock?
I love being outside, so hunting, fishing, camping or anything outdoors. I have fun with my family, dogs and friends. When I must be indoors, I’m watching the Cowboys.
Photo courtesy of Photo by Kevin Dietsch.