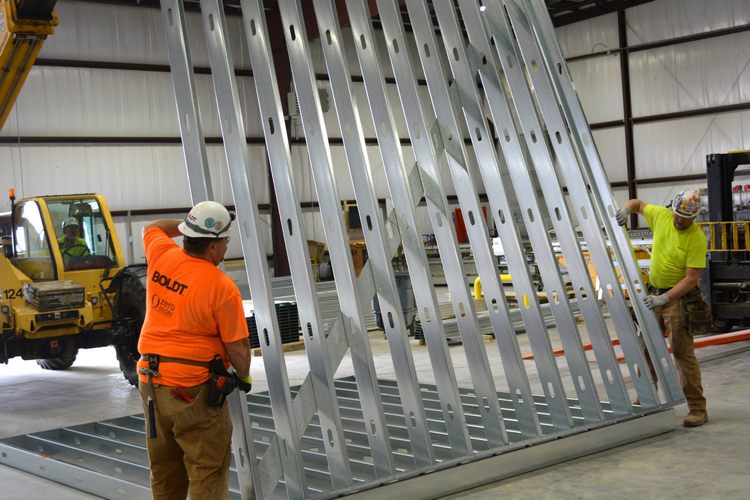
The University of California, Davis had clear construction goals for its new on-campus health clinic requiring an innovative approach. The 4,000-square-foot clinic, site utilities and site improvements had to be finished in seven months in time for the university’s open enrollment scheduled for November 2020. The budget for the primary care clinic was fixed and perhaps at odds with the timeline. And, just as construction started, the nation was in the midst of the COVID-19 pandemic.
For The Boldt Company and Design-Build partner Boulder Associates, the solution was a highly collaborative environment that made extensive use of prefabrication. This allowed construction crews to work concurrently on different elements of the building without jobsite staging conflicts.
For the project team, this meant earmarking a significant portion of the construction process for prefabrication and calling on a frequent partner, Mark III Construction out of California. The two companies had worked together on several construction projects, but this approach took it one step further by closely coordinating both the fabrication and installation work.
Prefabrication moved to Mark III’s 24,000-square-foot facility where social distancing was implemented into daily practice. Crews averaged 12-15 people, which was easier to control workspace distancing and wearing PPE than in the field. The facility layout promoted Lean construction processes with flexible work cells that provided seamless changeover for any trade.
To meet the tight timeline, crews manufactured all interior and exterior wall panels at Mark III’s MEP manufacturing facility before delivering them for installation onsite. This construction and delivery method allowed crews to cut installation time in half, while allowing production teams to move ahead with overhead assemblies onsite without overcrowding the jobsite. All overhead piping, plumbing hangars, electrical and in-wall assemblies for plumbing and electrical were prefabricated in the manufacturing facility, as were duct banks and conduit banks. This tactical approach shaved three weeks off the master plan on a 28-week construction schedule.
A primary concern was ensuring all the pre-manufactured systems matched the built environment, so teams turned to technology-based solutions. Both Boldt and Mark III used a geospatial station to map out connecting points and BIM was used to virtually build the walls. As a result, tolerances were within a fraction of an inch.
As of summer 2020, the project is on schedule for turnover to the owner in October 2020.