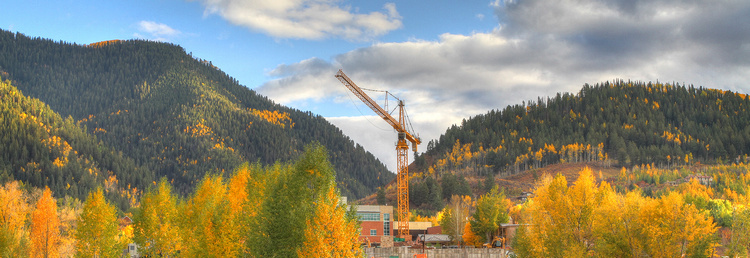
By David Hanen
Everyone is fascinated by mountains, with their rugged, majestic heights and sweeping vistas, but mountain construction projects face challenges of weather, transportation, labor and resources that don’t always arise in the flatlands. Here are some down-to-earth issues a savvy construction manager must consider when planning a high-altitude project.
Expect harsh, unforgiving weather
Mountain weather conducive to building projects is no guarantee at any time of year. Summers are brief, with monsoon rains and snowfall not unheard of; and winters are long, with extended periods of bitter cold punctuated by frequent bouts of heavy snowfall. That means if you have a project that will extend into winter, you’ll need a good idea of what to expect and how to plan for every whim of the weather.
Let history be your guide. Your mountain-building experience will tell you when it’s safe and efficient to start and complete various phases of your project. In general, work from the outside in, beginning in summer — typically mid to late June in high-mountain climates.
You’ll want to pour the foundation and erect the steel and framing in summer, and no later than early fall, so you can wrap the building before cold weather sets in. Once wrapped, the framework will retain heat so you can pour the internal floors and install sleeves and ductwork, then complete most of the interior finish during the frigid winter months.
Although it’s possible to use temporary roofing, it’s wiser to install permanent roofing material to save time and money from the get-go. Permanent roofing and its associated insulation offer practical benefits during winter, including interior heat retention and more efficient and comfortable indoor working conditions. And on the exterior, a permanent roof affords easier snow clearance and improved water drainage.
During interior construction in winter, it’s imperative to have a safe, reliable interior heat source. Gas heaters are ideal. You’ll want to develop a heating plan based on the structure’s cubic footage and access to natural gas rather than propane tanks, if possible.
It’s essential to have a well-thought-out staging plan in place, because high-mountain mud season in April and May can wreak havoc with even the best-planned building schedule. Rapid spring snowmelt, followed by foot-deep new snowfalls, are typical in the mountain environment, leaving construction sites mired in thick, slippery (or frozen) mud that can slow or prevent deliveries and services. To minimize mud at the site, you’ll want to build temporary walkways to avoid tracking mud into the building. Remove snow as soon as possible after a storm and store excavated material away from the building before it freezes. Keep access roads on the site clear and graded to the extent possible. Schedule sidewalk-pouring and similar tasks together after mud season and before the late summer monsoon season. In other words, build as fast as you can in the short time available to you.
Safety and regulatory issues
Now that fire season extends pretty much year-round in mountain areas, it’s essential to be hypervigilant for the potential for fires. Check with local fire departments, state and national park and forestry agencies, and other relevant entities about specific laws and regulations that might affect your project. Closely follow fire bans and state guidelines, and obtain appropriate permits for any work that may pose a fire hazard. Don’t allow any hot work outdoors — anything that creates a spark, such as welding, even just for cutting the head off a bolt, can ignite a devastating fire.
Use local resources and subcontractors
If you’re newly bidding on a mountain project, it’s a good idea to form solid relationships well ahead of time with local subcontractors who have the ability to tackle big projects and already know the territory. If possible, vet subcontractors up front, minimizing roadblocks or other issues down the road.
Resource allocation and local labor
Hiring employees with the necessary skills and experience can be a challenge, but if you can, hire local trade and craft people. Not only will you save money on housing and transportation, local employees feel exceptional pride of ownership in their work because they helped build a hometown project.
If you must relocate employees to the jobsite, try to find long-term accommodations ahead of time or offer an assistance package for hotels, furnished apartments or long-term rentals, and factor the costs of employee travel and relocation into your overall bid. Understand that the more desirable the area (think resort towns like Aspen or Vail), the higher the cost of employee housing will be, but the cost is usually a small price to pay for completing prestige work.
Mountain driving can be hazardous at any time of year, and snowfall, rock slides, fires, highway accidents and road work can impede travel and deliveries to a jobsite. Be sure you have a plan to ensure your workers and materials can get to work safely in the event of a highway or canyon closure.
Get to know the local town officials and leaders
Construction inevitably disrupts daily life in mountain communities, with noise, road crowding and often local resident resistance. So, well before the project starts — or even goes out for bid — cultivate friendly relationships with local officials and townspeople. Be open and transparent, and communicate frequently and honestly with all involved. These relationships will go a long way toward building acceptance for your project and can be invaluable when issues arise or you need a special permit.
Wrapping up
Can any company become a mountain builder?
Yes, it’s possible to break into mountain work, but first you need a thorough grasp of mountain seasons and what work you can and cannot do, and when. Summer is more forgiving but, even then rainstorms or early freezes, even snow, can affect a project and its timeline.
The big takeaway: plan as though your project depended on it…because it does.
Photos courtesy of Haselden Construction.
David Hanen, a superintendent at Haselden Construction, started building houses at age 14 and has worked in construction throughout Colorado’s Rocky Mountain Region for more than 25 years.