By Jillian Boeker
Hospital and medical facility renovations continue to boom and, while hospital executives and staff entertain a vision of the outcome of a construction project, how to get there is the responsibility of the general contractor, as well as the superintendent on the jobsite.
This responsibility includes working closely with facilities liaisons and staff to ensure operations – whether patient care or research – are not impacted. Owners rely on their contractor particularly on four key aspects: infection control, water infiltration protection plan, communications and scheduling and install verification. These elements are, of course, interwoven with safety – the most important priority everyone on the jobsite performs – for patients, staff, visitors and construction workers.
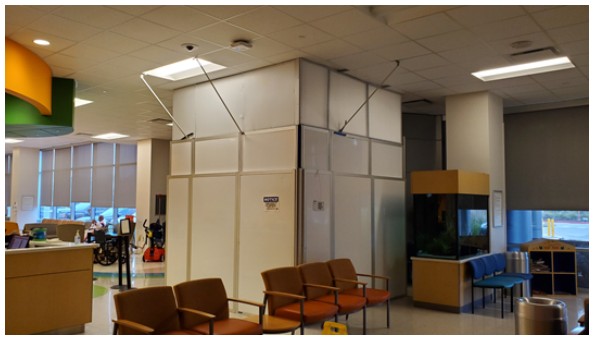
1) Infection control/containment/dust control
Renovations in active healthcare facilities can pose multiple hazards to staff, patients and the public throughout the facility. When planning to execute a successful renovation project, infection control and interim life safety measures are always top of mind. Working with facilities personnel to plan out the project activities is essential, as requirements may differ from facility to facility. The following are some best practices to take into account when implementing an infection control/interim life safety plan.
Infection control/containment
- Long term: The STARC System is a great long-term, hard-containment system that helps control dust and noise levels from within the project site. Another quicker and cost-effective solution for smaller projects is using fire-rated Cordek material and metal studs to construct walls, which gives a more professional and durable finish. It may also be needed to construct sheetrock walls with insulation to further prevent noise and provide a finished wall.
- Short term: When constructing a temporary system (three days or less), using fire-rated plastic material to construct a dust-tight barrier is quick and easy to erect and take down. For the more public areas, using Cordek is also a great option.
- On phased projects, it may be necessary to plan for both short- and long-term containment systems to meet the needs of construction.
Dust control
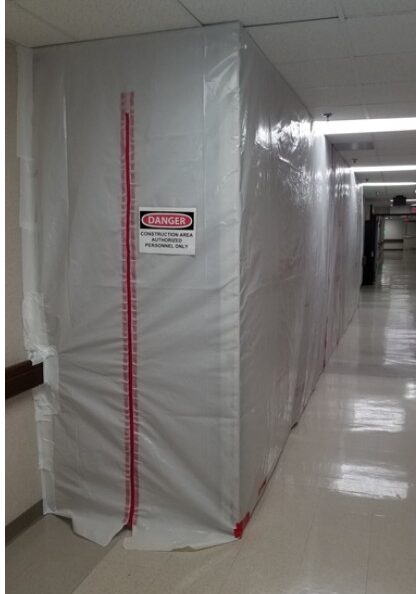
- Use of air flow monitors (manometers) or visual indicators such as the “ball-in-the-wall” device is useful to report and record the difference in pressure from the construction side and public sides of barriers.
- When working in an existing facility, such as a hospital, it is important to look at existing duct systems that run in and out of the construction space. When encountering a return air grille that feeds an existing air handling unit, filter media can be used to contain dust and ensure the existing air handling unit has the required return air flow. It is also important to investigate any penetrations that may exist within the construction area that will need to be blocked or filled in.
- The use of tacky mats placed at exits will help contain and prevent dust from tracking outside of the project site. When dust is heavy due to certain activities such as demo, it is best to use carpet tile within the containment that is slightly damp to help further prevent dust from leaving the jobsite.
2) Water infiltration protection plan
With every renovation, teams must consider the existing utilities running through the ceiling, walls and under the floor, because as work begins near exposed pipes, the possibility of water making its way into the space is increased. Therefore, a contractor needs to have a water infiltration protection plan. This plan addresses factors that affect the project’s level of risk such as weather, temporary protection measures, high-risk project phases (e.g., sprinkler tie-in, sanitary tie-in and roof work), pre-event plans, what to do in case of a water event and post-event plans.
The project site must have access to a WIPP cart (tools to manage an event) and have valve maps posted for use in the event of an incident. The facilities group can help by providing a valve map for the space to the contractor, as well as any information about sensitive areas near the jobsite. If a water event should occur, understanding the adjacent spaces will allow for effective response and containment.
3) Communication/scheduling
Constant communication is an asset to a project team before the project starts and as it progresses. Keeping the owner and facility manager involved in the scheduling of utility outages, critical activities and containment changes eliminates surprises and is key to a successful outcome.
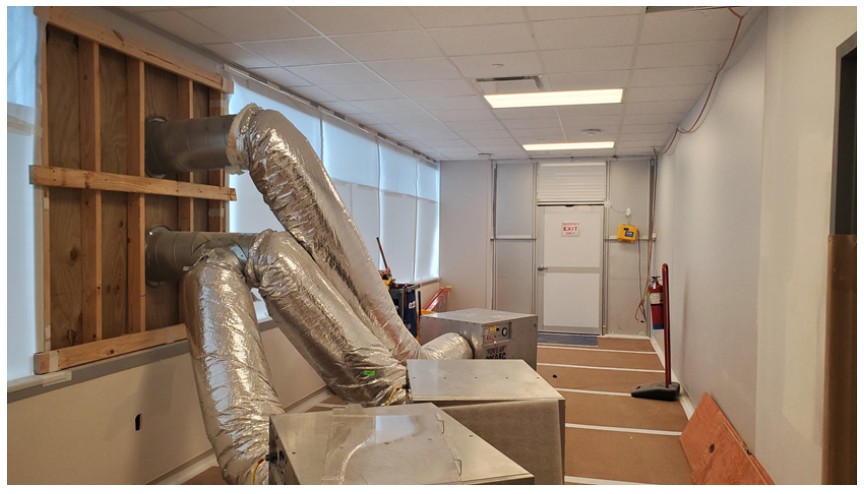
McCarthy Building Companies’ Superintendent Mike Broderick offers a key piece of advice for those working in active hospitals: “One of the most important items to look at is a lockout tagout program on all systems, including electrical, med gas, steam and all water systems. Especially in older hospitals, it is important to research all electrical circuits prior to submitting a shutdown request, because shutting off a breaker controlling a specific area could be tied into a critical patient care area or even an OR.”
Freight elevators and loading docks are often shared between construction and building personnel. Understanding high-traffic hours and providing delivery time requirements to vendors ensures the construction’s impact on the supply chain of the building is limited, or even unnoticeable.
During the project, it may be necessary to block off paths of travel to maintain the integrity of the infection control barrier. Water may need to be valved off to a specific zone during tie-in. An air handler may need to be restarted.
“In the infection control area, a site-specific daily checklist should be used to verify all areas of infection control are verified prior to start of daily tasks in that area,” added Broderick.
Distributing a two-week look-ahead schedule and an updated phasing plan to your team to provide notice, and discuss any scheduling conflicts, will help keep everyone on the same page and ensure that access is not limited for either party during these activities.
High-risk activities should be discussed as a group in advance. Some team members may be aware of specific requirements or have previous experience that will benefit the project. For example, on one of our hospital projects, there is a large void under the drive where we staged a crane lift. The crane had to meet specific outrigger requirements to keep it supported during the critical lift. This void is not visible from the surface, and the project’s structural engineer brought it to the team’s attention during a look-ahead meeting for critical activities. The crane’s specifications were provided and approved before the lift was scheduled.
4) First-install verifications
First install verifications are held with the owners, designers and end users after a specific elevation or detail is complete. For example, if a cluster of exam rooms has a similar sink and millwork elevation, building one for approval before proceeding with the rest allows all parties to see a full-scale finished product and approve the locations and quality of install.
In-wall verifications should be completed prior to the contractor getting their wall cover inspection. This gives the end users and designers the ability to confirm and approve the heights of electrical switches and outlets, locations of sinks, rough-in for equipment, etc.
Further, facilities should be given the opportunity to perform an above-ceiling inspection as well, prior to the contractor’s ceiling-cover inspection. This provides opportunity to confirm access to HVAC boxes, lighting controls and emergency valves.
Undergoing a renovation of a hospital, medical facility or research laboratory takes careful planning and communication involving executives, facilities, staff and the contractor. If all parties are clear in their expectations and plan, the renovation’s impacts on operations can be minimized and help ensure a successful project.
Jillian Boeker is an assistant project manager for McCarthy Building Companies based in Houston, Texas. She works onsite within the Specialized Solutions Group that focuses on healthcare renovations and specialty projects.