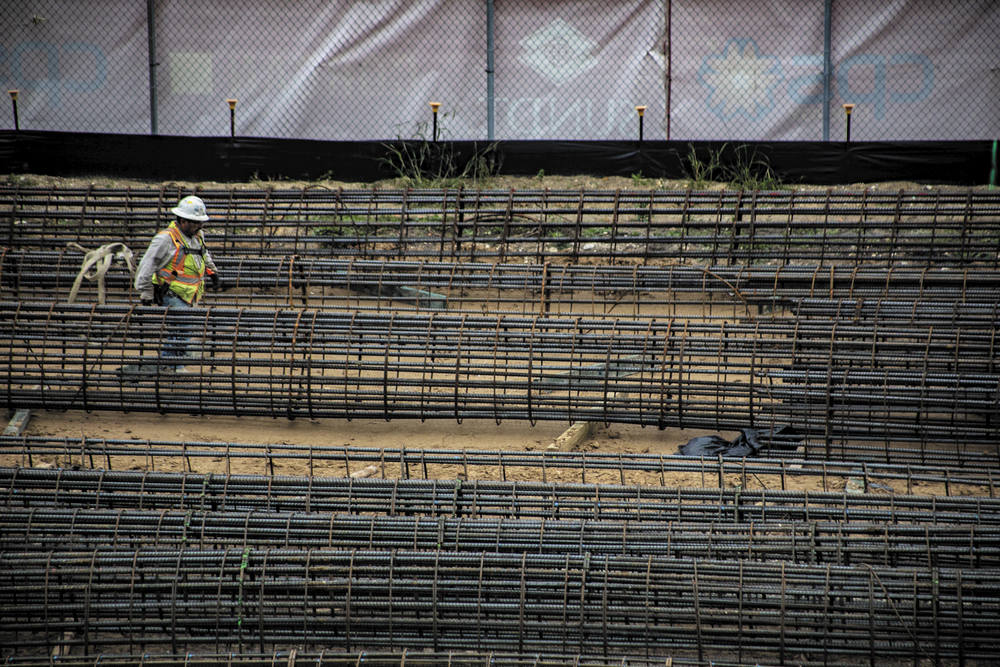
By Mark Hendricks
The last year has reinforced that nothing is certain, and the unexpected should always be expected. Major storms, growing labor shortages, a canal blockage and a global pandemic were just a few of the many unpredictable events that have caused procurement interruptions, longer lead times and rising prices for most of the commonly used building materials.
The inevitable slowdown put an uncomfortable spotlight on the construction industry’s heavy dependence on the global supply chain, as well as demonstrated how the shifting of just a few variables can cause major headaches. Delivery times for lumber orders, alone, have more than doubled over the last year.
A recent survey by the Associated General Contractors of America found that nearly nine out of 10 firms (88%) are experiencing project delays. Among these firms, 75% cite delays due to longer lead times or shortages of materials, while 57% cite delivery delays. The industry has seen major price spikes in steel and lumber, further hindering economic recovery. That said, construction demand itself has not stopped; in fact, the nation’s construction industry added 11,000 jobs on net in July, according to Associated Builders and Contractors, with nonresidential construction employment expanding by 2,900 positions on net. Thankfully, many firms have become adept at working around supply chain and pricing disruptions.
But construction is more than just delivering on time and staying on budget; it’s about keeping everyone’s safety top of mind, while ensuring the seamless flow of operations amid the daily disruptions of orange barrels and yellow tape. It requires general contractors and their project teams to understand what strategies can be implemented to work around material shortages, price hikes and other complications by utilizing a combination of new technology and good old-fashioned improvisation — helping to ensure the comfort and safety of crews, building occupants, etc.
The following are three key areas to consider when faced with unexpected shortages, nature-related setbacks or any other challenges that can cause major pitfalls for projects in markets across the country.
1. Preconstruction planning
Though you can’t predict when nature or unforeseen global pandemics could cause setbacks in your project timelines, utilizing effective methods of preconstruction planning can lead any team to overcome these challenges and maintain success for a project.
For one project in Pensacola, Florida, multiple hurricanes and tropical storms hit the area during a span of two years. This included Hurricane Irma, a Category 5 monster that forced the Hoar Construction team to take the crane down for a period of time. Despite losing 137 days off the original timeline due to the hurricanes, as well as an additional 14 feet of heavy rain, the use of preplanning with 3D modeling and prefabrication on MEP racks, storm piping, doors and headwalls led to an expedited topping out ceremony. The “end-to-beginning” pull planning approach provides clarity for all key decision makers and trade partners who need to identify key milestones and maintain a constant workflow, while advanced technology allows teams to get the job done faster than initially planned.
2. Think outside the box
Placing bulk material orders well ahead of groundbreaking, and leveraging newer technologies to track material prices and availability in real-time, can also help to mitigate the impact that supply shortages have on scheduling and delivery.
Keep in mind that when planning these bulk orders in advance, you must often find workarounds for material transportation and storage. This is where the unconventional becomes conventional, and teams are forced to think outside of the box. Parking garages can become temporary lay-down areas, helping to cut down on storage fees and transportation costs. Modular construction — for everything from bathrooms and patient rooms in healthcare construction, for example, to exterior skins — also neatly solves this challenge depending on the size and scope of the project, with pods or structures built offsite and inserted in place once complete. It’s also useful to collaborate with the architect during the design phase to work around long lead times for certain materials and to find alternatives, which have a much shorter procurement time. Getting in early in the preconstruction phase of the process like this ends up saving time later by eliminating costly redesigns.
3. Stay up-to-date
General contractors should stay up-to-date on supply chain trends and market activity while becoming a proactive partner with procurement managers, vendors and suppliers.
And, while it is nearly impossible to predict what materials will be impacted next, deploying a “real-time” tracking mentality can save valuable dollars when sourcing trade partners, navigating lock-in quotes and factoring in schedule changes due to supply delays. For example, knowing that waiting on steel delivery continues to be a challenge, you can work with the client during the schematic budget phase to get a release to put in a mill work order for steel before there’s even a final budget for the project. Getting in line early at the mill keeps you from experiencing that delay when the design is actually completed.
4. Embrace transparency + consistent communication
For superintendents in the thick of these challenges, staying proactive can seem like you’re chasing a moving target. But embracing transparency and consistent communication with trade partners, project owners and all other stakeholders, will help everyone feel more comfortable with today’s unpredictable environment and allow for faster, on-the-fly decision making when issues arise. Holding weekly meetings with all relevant trade partners at once can help everyone understand sequencing challenges and potential solutions. If a trade partner understands why material delivery is affecting their work schedule, they may be more willing to be flexible. And if an owner knows that you’re committed to juggling schedules and implementing creative solutions to unexpected setbacks, by keeping them informed along the way, they’ll be more confident in your ability to meet the project goals.
While supply chain shortages are certainly going to affect construction projects in the foreseeable future, the greatest challenge the construction industry faces is unpredictability — not knowing what our next greatest setback will be. Preconstruction strategies, and their associated technologies, are the guiding lights that can effectively counter that great unknown, and those who embrace their use are well positioned for future growth and success to weather even the biggest storms.
Mark Hendricks is senior vice president of healthcare at Hoar Construction.
Photo credit Robby Brown + Sundt Construction.