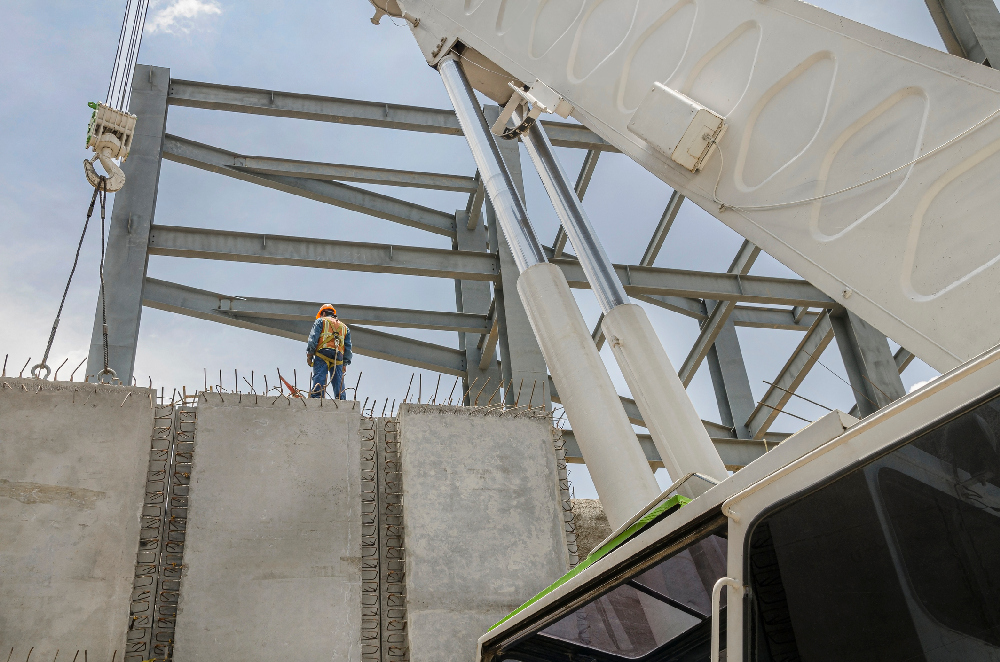
Safety best practices on the jobsite
By Lester Hill
Tilt-up construction is fast becoming the go-to method for almost all forms of industrial and commercial construction, from distribution centers, to schools, churches, libraries, retail centers and office buildings. However, it’s not without risks when compared with traditional methods of building. And when best practice controls are in place, risks can be minimized. The following tips can lay the groundwork for a safer process.
1. Lifting and erecting panels. Prior to commencement of panel erection, the contractor should ensure that detailed plans for lifting and erecting the panels are prepared under the direction of a registered professional engineer and made available on the jobsite. The site-specific erection plan should detail the process sequence, as well as lifting methods and procedures that don’t put employees at risk of being injured by a panel or other supporting equipment.
In addition, the site-specific plan for erecting panels should include an engineered-lifting plan outlining the crane capacity and all rigging types/capacities to be used. The lifting plan would evaluate all crane lifts and specifically identify any lifts that are deemed critical. A critical lift is typically defined as one that exceeds 75% of the rated capacity of a particular crane or derrick, or which requires the use of more than one crane or derrick, according to the Occupational Safety and Health Administration’s steel erection standard. Advanced attention should be given to these lifts to ensure they are planned properly.
2. Fall protection plan. A site-specific fall protection plan should also be required to identify fall hazards involved in the tilt-up process and how workers will be protected. In general, all workers exposed to falls six feet or greater will need to be protected by personal fall arrest systems, fall restraint systems, guardrails, nets or hole covers. The use of alternative work platforms, such as aerial lifts, will require specific fall protection methods that should be identified within the plan.
The erector’s safety plan should also designate competent persons for all processes including crane operation, rigging/lifting, bracing and all other procedures involved. The competent persons would be responsible for conducting inspections of all processes and equipment as required by OSHA’s construction standards and the project documents. Crane operator certifications and proof of crane inspections should also be provided within the plan.
3. General safety plan. Typically, the general contractor on the jobsite would outline the project’s expectations for safety and health of all workers. This would include subcontractors — especially those with the tilt-up erector. A pre-job meeting and survey of the site by the tilt-up erector and the contractor should be held to set expectations for the project.
The pre-job survey would include site access, casting bed locations, crane travel routes, crane placement, crane type/capacity, rigging capacities, bracing details and a formal review of the engineered drawings and site-specific requirements. This meeting should also include a discussion focused on coordination of other trades onsite, and where they will be permitted to work during the tilt-up process and when they will be permitted to access building areas after tilt-up members are installed. The contractor should get to know the tilt-up erector by asking for their OSHA 300 A log for the past three years and complete an OSHA Establishment Search on the erector to gain some insight into any history of OSHA inspections.
4. Quality control. To maintain proper quality control, contractors should keep a comprehensive record that includes an inventory of inspection records for all materials used in production, as well as shop drawings for the production and erection of products. The tilt-up contractor should develop a site-specific quality control program that outlines how they will comply with industry standards and project requirements.
5. Certifications. Another consideration to ensure a safer, quality project is utilizing certified contractors within the industry. To maintain a certification with the Tilt-up Concrete Association, a company’s personnel and programs/procedures are audited annually for compliance and safety. This audit will review a list of competent person designations who are responsible for safety on each project, as well as safety plan information with methods of determining, documenting and mitigating jobsite hazards.
A company should also employ at least one ACI Certified Supervisor or Technician. The general contractor should be responsible for either directly employing these qualified personnel or for ensuring that its subcontractors employ the required personnel. All subcontracts or purchase orders/agreements that cover the above-noted scopes of work must include statements requiring the subcontractor or vendor to meet these requirements.
In addition, at least one ACI Tilt-Up Certified individual should be onsite and either in direct control of the work being performed or participating in the production and erection operations. Evidence of compliance will be verified during a review of project documentation or actual onsite observation.
Lester Hill is senior construction specialist in Risk Engineering at The Hartford.