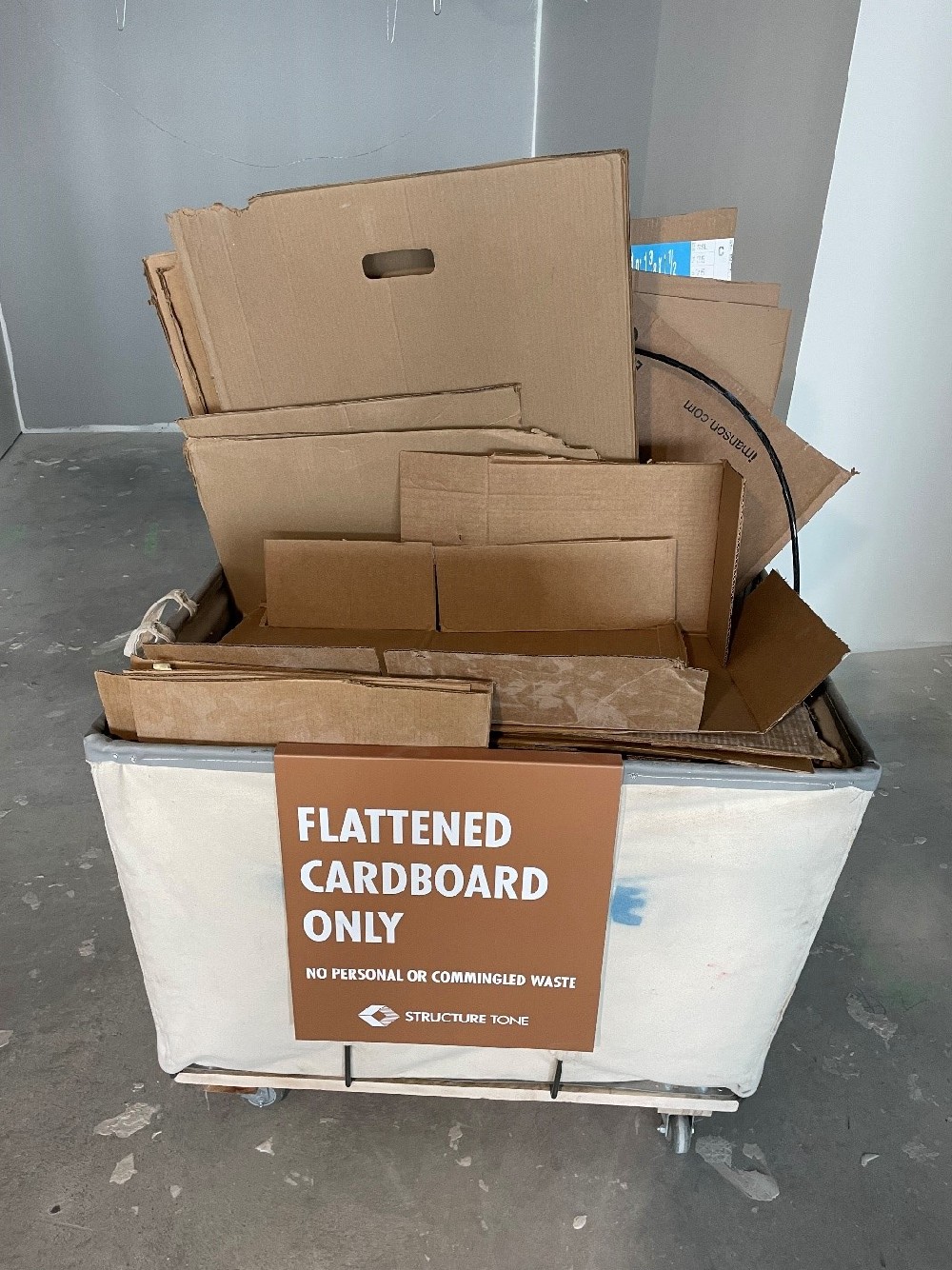
4 best practices from the field when pursuing LEED certification
By Michael Orbank
As the climate crisis worsens, the impacts of traditional construction and demolition waste disposal have begun to stick out like a dirty, sore thumb. Historically accepted commingled C&D waste practices are becoming unsustainable as the industry quickly realizes that the promises of high landfill diversion, and material recycling percentages from the waste processor, don’t quite match reality. The question is, how can the construction industry improve our waste practices to help promote a cleaner, more circular future?
Site separation is key, and superintendents play maybe the most critical role in ensuring this practice is implemented successfully on the jobsite. While adding one more task to the dozens of daily challenges superintendents face may not sound appealing, it’s quite achievable through early planning, meaningful collaboration, clear communication and trust in your laborers.
1. Early action: identify in preconstruction
Use the preconstruction phase of the project to identify the key waste streams expected of the project. For example, the typical types of waste in a large commercial interior renovation project are scrap metal, clean gypsum wall board, cardboard and plastic packaging wrap. Once those categories are identified, the team can develop recyclable metal waste signage for onsite hampers dedicated to each targeted stream, as well as signs for commingled waste (everything else). During subcontractor buy-out, add language into subcontracts to clarify that site separation will occur. Not only does this process help facilitate a Lean-style approach to construction, but it also helps the project meet (and often exceed) green building requirements.
2. Site implementation: add bins and clear signage
As mobilization and enabling begins for a project, ensure hamper and signage delivery is timely and walk your subcontractors through the process and simple logistics. For a recent seven-story, 225,000-square-foot interior fit-out in Boston, Massachusetts, the superintendent brought the company’s sustainability manager to the first subcontractor foreman’s meeting to explain the program, the desired outcome and physically show them the signage so they could, in turn, explain it to their laborers.
This is where superintendents can have the greatest influence: talking to and trusting the laborers. Tony Ferrara, the head superintendent on the Boston project, says he “had faith in the laborers and asked them to help.” His faith paid off, as before long the process of separated waste collection became typical. To make sure that the specified material streams were separated, onsite laborers developed a system in which they claim no extra time or effort is required. Hampers with labels are delivered to each floor based on the construction schedule and, each day, singular material streams are collected into these labeled hampers and kept onsite until enough of that material is ready for a 15/20/30-yard dumpster that week.
3. Communication: explain the “why”
With the jobsite team on the same page, the project team should also inform other key project partners about the program goals to make sure the process moves smoothly.
- Property manager. Scheduling pickups with the property and making sure access is available is key to making sure you can maintain buy-in with field staff. In a tight urban location, for example, a busy office tower with several major construction projects means that loading dock access needs to be coordinated.
- Waste haulers. Regardless of site separation, every jobsite will have dumpsters coming and going on a regular basis. Discuss the site separation needs with the waste hauler to identify a recycler for each of the targeted material streams. Once that is established, the superintendent should be able to call for a pickup, specify a material stream and let the hauler take care of the rest.
4. Avoid pain points: lessons learned
Site-separated waste materials need to be uniform and uncontaminated and should represent a majority of the waste stream for a given project. To avoid the pain points of load contamination, double handling waste and process apathy, consider these tips:
- Don’t leave hampers unlabeled and open onsite. Set up a process that maximizes efficiency and gives little room for mistakes. Ask for labor input and suggestions.
- Work with the subcontractors so they understand the intention of the program and buy into the process. Center piling materials like cut drywall, scrap ductwork and carboard boxes from finish materials is key to helping the laborers ultimately separate waste. Stay firm and reiterate that programs like this need to be mandatory throughout the jobsite.
- Always keep commingled hampers available. Not everything will fall into the targeted material streams and that’s okay (for now). Remember the mantra “When in doubt, throw it out” and don’t let perfect get in the way of better.
- Get creative with your space and seek help from your team. Not all projects have thousands of square feet to store hampers, but working with the hauler and the property manager can generate new possibilities and solutions.
This process isn’t rocket science, but it is different from typical disposal. It can be overwhelming to think about how much changing processes can interfere with project delivery, labor costs and schedule impacts… but it doesn’t need to be.
Superintendents understand the jobsite better than anyone, and success for programs like site separation depend on insight and creativity. Set up the project documentation, educate all partners of the “why” and understand that this is a new idea to most of the industry. By providing a helping (yet firm) hand, creating buy-in across the project team and allowing for creativity, the once imagined herculean effort of site separation transforms into a simple process change.
Michael Orbank is the sustainability manager for the Northeast Region of STO Building Group.