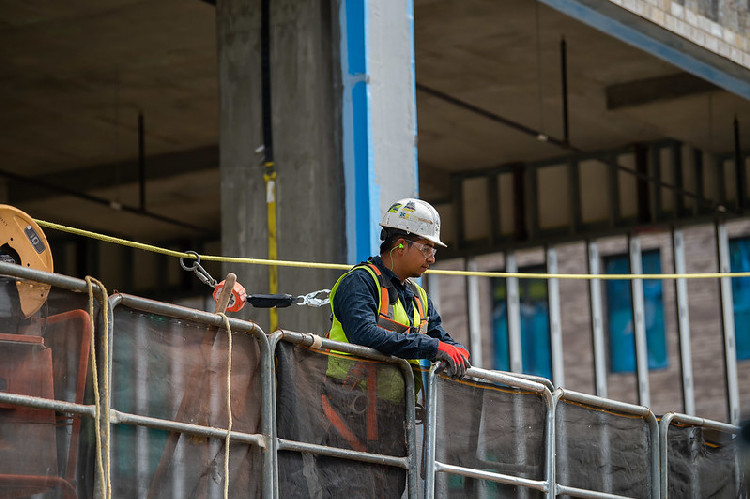
Navigating inspection, recertification standards for fall protection
By Phil Jacklin
In the challenging field of work-at-heights, compliance with inspection and recertification standards isn’t just about ticking boxes — it’s pivotal for ensuring worker safety and organizational resilience. And, as a superintendent, it’s important you’re in the loop about these vital regulations.
Understanding fall protection inspection standards
The following inspection standards are fundamental for maintaining equipment integrity and ensuring the safety of your crew on the jobsite. For this reason, many of these practices are required for compliance with consensus standards, including the ANSI/ASSP Z359 Fall Protection Code Package. In addition, many regulatory jurisdictions require inspections as outlined below, including OSHA 1910.140, 1910.27 and OSHA 1926 for construction worker safety.
- Pre-use inspections. Before each use, fall protection must be inspected for wear, damage or defects. The meticulous eye of the user can catch immediate risks, making this step non-negotiable for every equipment piece, every time. Pre-use inspections pertain to permanently installed systems, as well as PPE and non-certified anchorages. For PPE inspections, users should consider these basic elements of a thorough inspection: indicators, stitching, labels, webbing, hardware
- Indicators: harnesses have impact indicators that show if the harness has been loaded. Check the impact indicators first.
- Stitching: Check for any frayed or broken threads where the components are stitched together.
- Labels: Every fall protection harness will include a label that shows the weight rating, compliance standards, manufacturer and other information. Ensure the label is intact and legible.
- Webbing: Check the straps of the harness for any sign of damage or wear.
- Hardware: Check hardware for any sign of impact or damage.
- Annual inspections. All fall protection equipment must undergo comprehensive annual inspections. This includes reviewing these devices for signs of stress, wear and functionality, thus ensuring their readiness for the year ahead. In situations with equipment that is used multiple times a day and/or exposed to harsh conditions, more frequent, documented qualified-person inspections should be considered. In some instances, monthly or quarterly inspections may be appropriate.
- Semi-annual checks. In California, for example, the Code of Regulations requires an even tighter schedule with inspections mandated every six months.
- Suspended access anchorage 10-year recertification. For permanently installed suspended access anchorages, decennial re-certification is required. In many cases, the original documentation is missing and last date of certification is unknown; in these circumstances, a horizontal pull-test is performed to produce the certification and report.
While inspections are crucial, documentation is an often neglected, yet essential aspect of the overall process.
Documentation matters
Many organizations lack proper documentation for their fall protection equipment. This oversight isn’t just administrative, but poses significant risks some may not be aware of. While it requires a commitment to thorough record-keeping from the start, the following documentation considerations should be made for any managed, comprehensive fall protection program.
- Manufacturer’s instructions. In many instances, regulations and standards instruct employers to follow the manufacturer’s instructions for compliant use of fall protection equipment. When the language of the standard is incomplete or vague, courts and regulators often refer to manufacturer’s instructions to determine compliance.
- Equipment history. Documentation outlines fall protection service history, prior inspections, repairs and overall condition. Without this data, it’s difficult to assess the equipment’s reliability and compliance status, which can lead your crew to make uneducated decisions about the safety of a piece of equipment.
- Cost implications. Lack of documentation can lead to immediate expenses from urgent repairs or replacements, leading to hidden costs and potential downtime and delays for your team. Decisions made without historical data not only incur unexpected expenses, but also risk compromising long-term safety and compliance. Apart from direct costs and fines, good documentation proves the existence of a compliant program and reduces liability exposure.
- Compliance assurance. Thorough documentation is fundamental to ensuring fall protection equipment and programs adhere to strict compliance standards. As mentioned, it serves as tangible proof of compliance, thereby safeguarding your company from potential legal and financial ramifications linked to non-compliance. But in many instances, documentation requirements are explicit in the regulation and standards. These may include:
- Inspection documentation for the activities described in the section above
- Testing and re-certification documentation as described
- Worker training and re-training for authorized users of fall protection equipment and qualified persons for the installation and design of fall protection systems, temporary or permanent
Adopting a systematic approach to documentation ensures a traceable history for every equipment piece. Such proactive documentation practice eases the inspection process and fosters informed decision making, safeguarding you and your crew, as well as your organizational assets.
Elevating safety takes more than compliance
With stringent standards and frequent inspections, fall protection compliance is non-negotiable. While this may be an overwhelming read as a superintendent, you’re not expected to memorize all of these rules. That’s why a fall protection program serves as an aide to navigating safety compliance.
Finally, it’s crucial to remember that worker training is the silver bullet for safety. While programs are critical and required for compliance, the best advocate for worker safety is you.
Phil Jacklin is continuing education program manager at DFP.
Photo courtesy of: Associated Builders and Contractors