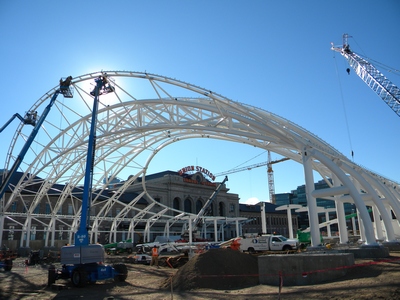
WINSTON-SALEM, N.C. — Steel Erectors Association of America announces the winners of its annual Project of the Year competition. Winners are selected by an independent panel of judges. Four companies were recognized in 2013.
“Since the contest’s inception more than 10 years ago, SEAA has recognized complex and unique steel erection projects throughout the world. Past projects demonstrated successful completion while overcoming unusual conditions, tight time constraints or other challenges. The 2013 winners reflect the importance of safety while sticking to the job’s schedule,” said Tom Underhill, executive director.
LPR Construction Co., Loveland, Colorado, for Denver Union Station Train Canopy. (Class I—Under $500,000)
The visual centerpiece of Denver’s transit center project in Lower Downtown’s residential and nightlife district is the canopy of Train Hall. The sculptural canopy is supported by a skeleton of steel tubes, a curving structure that is 70 feet tall at each end and 22 feet tall in the center. Its length is nearly 1-1/2 football fields long.
LPR Construction worked within a 10-month long erection process that had to be precisely orchestrated as the project involved extremely tight site constraints, and concurrent construction of the RTD bus station within the footprint of the Train Hall below grade. The canopy is held up by 32 arched cantilevered steel trusses of various lengths and 11 arched steel trusses that span 176 feet and are raised about 18 feet above the pedestrian level. The trusses are held together by thousands of pinned, bolted and welded joints and are supported by A-frame “kickstand” column pairs that cantilever out of the ground and carry the loads down to the pile foundations.
To erect the interior-most trusses, LPR Construction utilized a single shoring post and guy cables to stabilize and erect the first truss in two halves. The remaining nine trusses were erected in a single full-length piece. Each subsequent full-span truss was tied back to the preceding truss with permanent bracing prior to release of the crane and the two were stabilized as a pair. By combining this well thought-out strategy with careful execution, LPR was able to control direction and flow of erection by utilizing permanent bracing and eliminating the need for additional temporary bracing.
JPW Structural Contracting and JPW Erectors, Syracuse, New York, for the Destiny-Regal Theater in Syracuse. (Class II—$500,000 to $1 million)
Regal Entertainment Group wanted to add IMAX and RPX theaters to the company’s 17-screen complex in time for the premier of “Superman: Man of Steel.” Remaining on schedule was a priority in order to meet with the release of the movie. The challenge was to complete work while the mall remained fully operational during the harsh, winter months. All steel was erected in the blind. Many pieces weighed 11,000 pounds and the crane was lifting at close to maximum capacity at its 300-foot radius.
JPW worked closely with mall management and security to coordinate traffic (22 million people annually visit the sixth largest mall in the U.S.) where a 300-ton Link-Belt crawler crane with 400-foot boom was assembled, operated and disassembled.
The project consisted of removing 16,500 square feet of roof, raising it 50 feet and adding two additional floors. In addition to the challenge of working in close proximity to the public, severe cold weather threatened to hinder production. Wind chill was such that, at times, workers were limited to one-hour shifts to avoid frostbite. Snow and ice formed on flanges, in webs of beams and on decks making an already dangerous job even more so, requiring the areas to be cleaned before work could begin.
J.P. Cullen, Janesville, Wisconsin, for the Deep Space Auditorium in Verona, Wisconsin. (Class III—Over $1 million)
Deep Space is an 11,400-seat auditorium for Epic Systems Inc., a medical software company in Verona, Wisconsin. The auditorium was built for the company’s Annual User Group Meeting, monthly staff meetings, and events on the 811-acre campus. The 830,000-square-foot auditorium contains more than 17,000 tons of structural steel.
Epic wanted the auditorium to look invisible, as if it were a cave carved into a hill. Deep Space stands 5 stories tall, but from the southeast it appears to be below ground. From the west, a glass curtainwall with stone façade resembles a natural cave. Deep Space also features a 6-acre rolling green roof allowing people to walk on top of the building. The roof is a free span design measuring 110 feet wide at the front and more than 650 feet along the back radius with trusses spanning up to 280 feet.
JP Cullen’s team developed an unconventional solution for constructing the roof. Steel erection began with assembly of the auditorium’s long-span roof on the ground of the 80-foot deep “hole” in which Deep Space was constructed. That was followed by erection of the surrounding 5-story structure. The 9 million pound roof system was lifted vertically with strand jacks from the ground to its permanent location. Constructing the roof on the ground provided safer access to the work. It also allowed mechanical, electrical, plumbing and fire protection trades to install all their systems within the roof, as well as steel for catwalks and audio-visual supports, prior to erection of the roof itself.
Scheduling proved to be one of the biggest challenges of the project, given its complexity and the owner’s timeframe. Integrated Project Delivery was used to supply the steel to the site in the quickest possible manner. At peak production, more than 1,000 trade workers were on site. Ultimately, detailed planning and coordination proved successful as the project was delivered in time for the Annual User Group Meeting, an event that brings thousands of Epic’s clients from around the world to Verona. The Greater Madison Convention & Visitors Bureau estimates the economic impact of User Group Meeting at $6.5 million, second only to the World Dairy Expo.
Honorable Mention: Peterson Beckner Industries, Houston, Texas, for the ExxonMobile Campus Project — Energy Center in Spring,Texas. (Class III—Over $1 million)
The Energy Center is the gateway to ExxonMobil’s new office building campus that will house approximately 10,000 employees. The entire project consists of approximately 20 buildings, including low-rise offices, parking garages, a wellness center and child development center. The Energy Center is the architectural gem of the complex.
Energy Center consists of 180-by-180-by-50-foot-tall steel framed, glass-enclosed structure perched on 60-foot cantilevered sections of two opposing 210-by-90-by-100-foot-tall structures. Framing included heavy built-up box members up to 4.5-inches thick.
Central to Peterson Beckner being selected for the project was the development of a project-specific safety plan that provided safe access for employees of PBI, as well as ExxonMobile and general contractor, Gilbane/Harvey. PBI’s safety plan featured a scaffolding system that enabled safe access to specific connection points and transport between work points. The entire system was engineered and the steel fabricator attached hundreds of clips for scaffolds, individual retractable reel safety devices and horizontal lifelines.
According to Craig Peterson, project manager, “Probably the most daunting task was to properly position the heavy node weldments, which in many cases had six members framing into them. If the columns weren”t kept close to perfectly plumb, and all bearing surfaces properly seated, the geometry of the framing of the heavy-braced lines above would result in major problems down the line,” he said. Careful attention to placement of mill to bear members and proper welding procedures resulted in final location of cube trusses, including expected deflections, within 1 inch of theoretical in all directions.