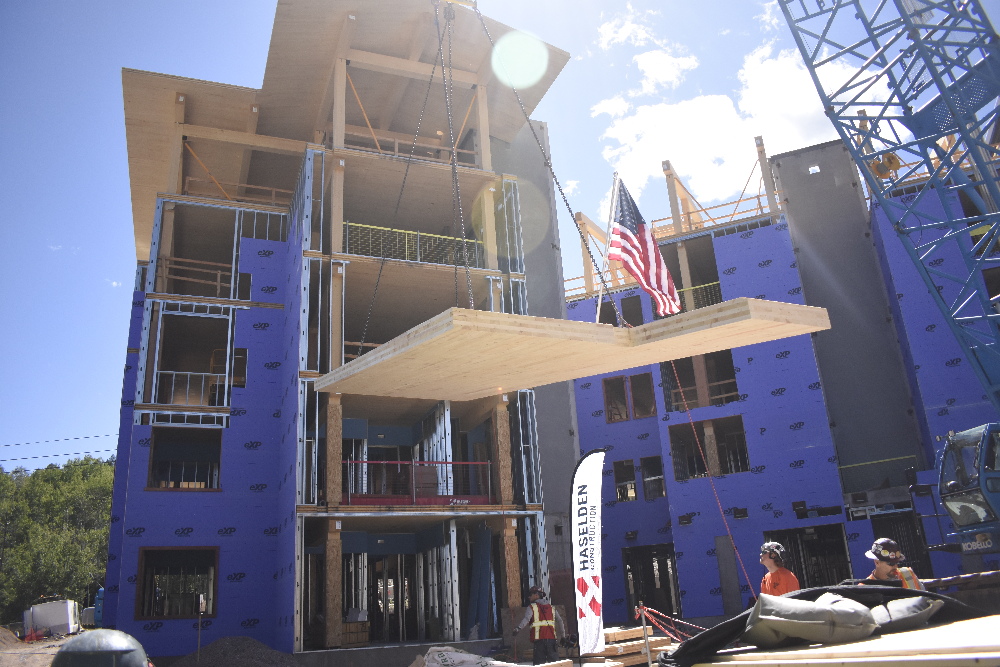
Mass timber: challenges + best practices
By: Derek Smuin
Mass timber construction continues to grow across the United States as an alternative to steel. Visually stunning and sustainable, this method presents a ton of benefits for both contractors and owners. For instance, its lighter weight makes for smaller, less expensive foundations and allows for a faster installation with a smaller workforce. Not to mention its environmental benefits, requiring less energy to produce, transport and even capture carbon long into its lifespan.
Although mass timber can serve the same purpose as steel, the approach to planning and construction is entirely different. As my team and I are wrapping up one of the first mass timber projects in the Rocky Mountains, I’ve learned how to adjust our approach to match this construction method.
Early coordination is key
Part of the draw of mass timber, in general, is that it’s a structure designed to be exposed. This is also where many of the challenges lie. A great building begins in preconstruction, and that’s especially true for mass timber. Collaboration between project stakeholders and subcontractors at all stages is required, as each has a role in the project’s success.
Involving the construction team at project kick-off ensures all the details are accounted for before construction begins. Each panel, column or glulam is manufactured specifically for the project to the precise measurements, so all coordination must be completed early. Due to this customization, manufacturing times can be longer than regular structures, making early coordination even more crucial.
Work with all subcontractors and trade partners to ensure each MEP system has been reviewed and coordinated to avoid clashes and meet the design specifications. Anything that needs to be moved after manufacturing, such as a light, must be patched, resulting in a clunky finish. Once the coordination is complete, the preconstruction team can determine if it’s necessary to procure any mass timber elements early to ensure they’re onsite at the correct time.
Understand final finishes
Another crucial aspect of preconstruction planning is understanding the final finish of the mass timber product. Each wood type has unique finishing characteristics that can significantly impact the appearance of the exposed pieces. We recommend ordering samples from manufacturers to allow the design team and owner to make an informed decision. This not only ensures the correct material is ordered, but also reduces the risk of rework. It’s important to remember that some finishes may accentuate natural wear in the panels, such as imperfections or transport-related wear. Additionally, each wood species has different structural capabilities, which should be considered during the design phase.
Assess site conditions, design specifications and code requirements to ensure the material selected will be viable for construction. Constructability reviews are vital to ensuring the building will be structurally sound and coordinate correctly with any other structural system. Although rare, sometimes mass timber works in tandem with steel or concrete to meet certain code requirements. Understanding how these systems connect and the order of installation before construction starts helps you manage each process during construction.
When building the schedule, allow extra time to finish the panels, as they may require finished sanding to get the most professional look. Once the panels, columns or beams are installed, sanding and repairs are challenging and create significant dust and particles. Planning for finish sanding also minimizes the risk of any damage or dings from transportation.
TLC for transportation, lay down + installation
Mass timber also requires more care throughout transportation, lay down and installation. Wood is more susceptible to damage, requiring more protection even through installation. Work with the manufacturer to ensure adequate security during transportation. Often, the panels travel hundreds of miles, opening more opportunities for damage. Once they arrive in the state, our team works with the erector to secure a separate laydown lot from the project. In our experience, construction sites are too tight to be able to store the panels onsite and ensure they are well protected. The separate lot allows them to remain protected and safe from other construction activities. Then, only the panels for the day’s installation are delivered each day, which prevents a crowded site and protects the panels.
Once the panels and columns are installed, they must be protected as construction continues. Like transportation, the wood can be damaged from accidental collisions, dropped tools and other construction activities. If any panels will be in direct sunlight, plan for sun protection, as the wood can bleach during construction, resulting in an uneven finish. Protecting the panels and structure early on helps to minimize the finish sanding later in the project and create the most professional finish.
Mass timber will only increase in popularity as technology improves and contractor experience grows. Its benefits make it an extremely attractive method: biophilic elements for its eventual residents, renewable manufacturing processes, carbon capture and more. Even for contractors, mass timber presents benefits. After building my career on traditional building structures, I’ve been impressed at the speed and durability that come with mass timber. And correct planning and care during construction can benefit all project stakeholders involved.
Derek Smuin is superintendent at Haselden Construction.
Photos courtesy of Haselden Construction