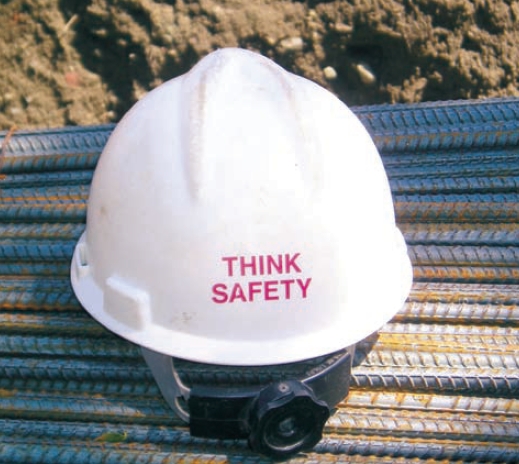
By Doug Henderson
During my normal day of visiting construction sites and conducting safety surveys, I see countless bad habits that result in safety violations. I”ve been given a long list of excuses for these habits, such as, “I didn”t know that was a rule,” or “that will make the job take twice as long.” I”m sure that we will all agree there is no good reason and no valid excuse not to be safe. Regardless of the underlying cause or condition, we need to ramp up the attention we place on safety, specifically with training and consistent enforcement of rules and regulations.
I believe many of the unsafe practices I see at the worksite are the result of complacency. A complacent employee is often too confident, overly at ease and satisfied with a situation, thus blinding them from the possible dangers and risks. Complacency leads to an individual becoming unaware of his or her surroundings and causes bad habits to develop that places their fellow workers in harm’s way.
As a safety director for a Detroit, Michigan-based general contractor, unfortunately I see many workers that I”d put in the category of complacent, this includes workers who are:
- Lazy. The person that is just plain lazy, they exist, I see them daily. They have many excuses for not following the rules, “My hard hat is in my truck, I”ll get it at break time,” or “do we really need to cover those holes in the floor today?” or “the pins for the scaffolding?, I”ll have those sent out in the next couple of days.”
- Unconcerned about others and how their behavior will impact overall job safety or the productivity of the project.
- Unwilling to learn or adapt to safety standards that will help save them or others from injuries.
- Stubborn, such as those workers who”ve been “doing it this way for 20 some years” and not eager to change their habits.
- Hurried, skipping steps believing a short cut is the better way to achieve their work.
The above excuses of bad behavior are just not acceptable. When laziness is tolerated, it can lead to injury or death. We need to stop these types of workers from what they are not doing and demand that they adhere to the necessary safety requirements of the job.
It is critical that management take the first step. Site supervisors must be firm and consistent with safety rules from the beginning of the projects. Managers must set expectation early and stay committed to enforcing the rules, even when it is inconvenient or costly. While it might be advantageous to look the other way, we can”t let lazy workers get by with bad behavior. Once bad habits are established, it’s difficult to change precedent.
Unconcerned workers are another problem on the jobsite. These workers are often bored and uninterested in their work. They especially can”t see how their poor safety habits may impact others or the overall productivity of the project. Telltale signs of the unconcerned workers include :
- They never clean up after themselves
- Not organized
- Contaminate the site with clutter, litter and debris
- Do not use the tools or equipment correctly
In this case mindless behavior is just as dangerous as choosing to make an unsafe choice. Carelessness isn”t without consequences. In fact, a worker who doesn”t care about his or her work practices can cause great harm to other workers or endanger an entire jobsite.
As managers, we must include and repeat safety as a high priority during our planning and follow through with execution. It might be beneficial to review inappropriate behavior and safety violations at a regularly scheduled meeting. Persistence is the key to eliminating laziness on the job.
Stubborn people are hard to deal with both on and off the job. You may hear them say,
- “I”m just not willing to do that.”
- “Why do I need to attend a tool box talk?”
- “Training… not interested.”
- Don”t bother me with that nonsense, I”ve been doing it this way for 20 some years and never had an accident yet.” (Keep in mind the most important word in that sentence is “yet.”)
These workers are simply not willing to change or learn new safety practices. I”ve even heard these types of comments from the subcontractor’s foreman or others who are considered to be the competent and responsible person on our sites. If the leader of the crew believes, “that we do not have time for safety,” he or she is the wrong person in charge of installing your work. The resistance to safety or the overall resistance to change can be present in all types of workers. We need to make safety a condition of employment at all levels.
Then there’s the “short-cut person.” This worker may find out that taking a short cut at work can result in the “shortest “way to the 24-hour emergency clinic. While that worker might get patched up and quickly return to the jobsite, cutting corners can often result in a more serious injury. For example, I know of one East Coast electrician who did not take the time to set up his ladder correctly, choosing instead to lean the ladder against the wall. That practice is never the correct use of a ladder, which the electrician found out when he fell and received a compound fracture to his leg. This “short-cut” worker found himself off the site for 12-16 weeks recovering from this painful incident. Cutting a few seconds here or there can change a worker’s life permanently and potentially end a career.
During my daily visits to construction sites, I have many opportunities to review the habits of countless workers. My primary concern is ensuring that everyone is performing his or her job in a manner that is safe and productive. Oftentimes I”ll bring our loss prevention specialist to the sites in an effort to find new ways to prevent accidents or incidents that could occur. When time allows, I also set up MIOSHA/CET visits so that we can help further educate workers and managers on the topic of safe habits for the worksite.
My experience proves that training, enforcement and monitoring safety behavior will help reduce injuries and fatalities related to construction activities. Such safety programs and policies work because they are borne out of real-life incidents, accidents, injuries and fatalities. We all need to accept and adapt to these changes and workplace practices that are necessary to make our construction sites a safe and healthy place to work. Our goals should be common, “zero fatalities, zero injuries and zero lost time.”
So how do we deal with complacent workers? Set the expectations for safety at the beginning of the project. Review the site rules. Talk about special conditions on the site. There will be times that the complacent person will need to be dealt with through pre-determined discipline procedures. Be strong and consistent with your safety programs.
Lofty goals? Yes, a BHAG (big hairy audacious goal). Sound safety programs and good safety habits will keep workers on the job and away from the emergency clinics. Let’s not add to the already growing industry statistics relating to construction accidents, deaths and injuries. We must all make safety a priority in our everyday routines. This includes providing quality PPE and training programs along with a safety culture that sends a strong message of zero tolerance.
Doug Henderson has worked in the construction industry in Southeastern Michigan for more than 35 years. He works with MIOSHA/CET and Insurance Loss Prevention to develop and enforce safety programs. Henderson can be reached at dhenderson@achse.net.
.