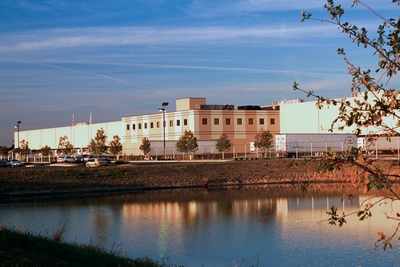
The Hershey Company’s corporate vision demanded an immense facility that required precision and innovative construction solutions. The job called for 1.1 million square feet of efficient space and a constant, 60 degree temperature with 50 percent humidity. This structure supports, receives, stores and ships $1 billion of chocolate each day.
An ambitious undertaking to say the least, constructing this facility called for 1.1 million square feet of warehouse and office space. The warehouse environmental criteria required a constant 60 degree temperature and a 50 percent relative humidity level. Logistical operations required warehouse structures capable of supporting massive loads while still keeping areas open for high-speed forklift traffic to move products. The Hershey Company needed emergency operational capabilities and safety systems to protect the $1 billion of chocolate in the facility in a given day.
Completing the job
Through the process of interactive collaboration, The Hershey Company’s leadership worked in coordination with The Korte Company to define the requirements of the job. With the critical information in mind and open communication between all parties, the mechanical Design-Build teams reviewed the preliminary layout provided by the owner and their consultants and went to work.
The result was a more efficient cooling system that eliminated nearly 20 percent of the rooftop units that were originally prescribed. The reduction of rooftop units also translated to long-term energy savings and a lower operating cost for the facility.
Reducing risk
By working closely with a comprehensive commercial risk company, the team was able to create efficiencies in risk management. A partnership with Factory Mutual facilitated Design-Build solutions ultimately decreased long-term insurance costs. In other words, Hershey achieved notable insurance savings through better Design-Build solutions.
One of those solutions included maximum foreseeable loss firewalls. To minimize risk, the overall building was subdivided into three separate sections by using double three-hour fire-rated MFL walls. The MFL walls were designed to allow the collapse of the entire structure adjacent to the wall without affecting the structural integrity of the remaining wall. The team also provided an independent fire protection system, including two separate 250,000-gallon water tanks, as well as an emergency system to provide backup power.
Maximizing workflow
To maximize workflow throughout the facility, the team collaborated with owner-contracted consultants to design a dynamic floorplan, and then constructed it to minimize product travel and handling. Additionally, rack and dock equipment was coordinated through owner-contracted vendors and installers, interfacing third-party timetables with the master construction schedule.
Specially formulated Type K shrinkage compensating cement was used in the bay areas to support designated high traffic and load specifications, while trap-rock-hardened concrete was used to handle the immense rack loads throughout the other areas of the facility.
Building for the long term
Hershey had a corporate vision to create an efficient, state-of-the-art distribution center. The project is a lasting example demonstrating how a corporate vision can drive design and construction solutions. The bottom line on this project was improved by project efficiencies. And long-term efficiencies are delivering cost savings throughout the life of the building and the operational functions it serves.
Source: www.korteco.com.
Photos courtesy of Dennis Calvert.