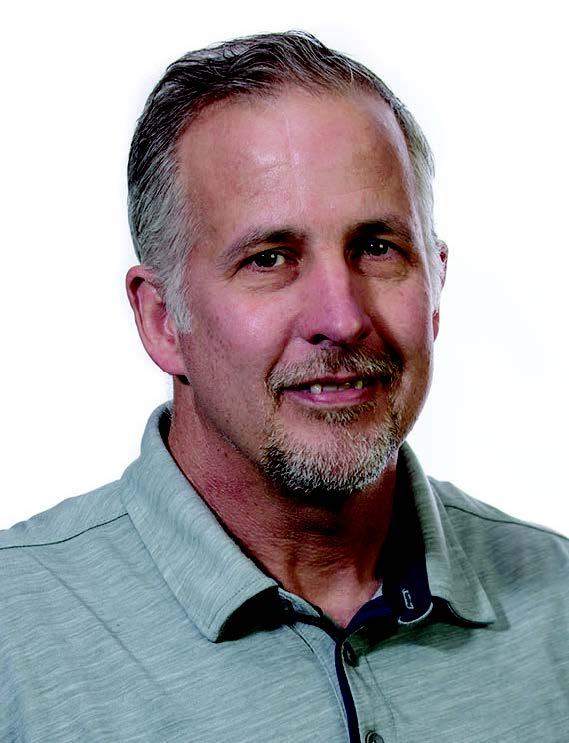
Establishing, maintaining successful working relationships on the jobsite
By Chris Maday Schmidt
Casey Blake is a project superintendent with BNBuilders and 30 years of experience in the construction industry. Much of Blake’s experience has been in the construction of large corporate headquarters, life science, healthcare, education and commercial construction projects. He has extensive experience with contract negotiations, estimating, building codes and regulations, materials purchasing and site management. Join Construction Superintendent as Blake shares what’s new in the industry, key takeaways about Lean and green and the attributes that make up a quality super.
(Q) What is the biggest difference you see in the industry today compared to when you started in the field more than 30 Years ago?
No question, the biggest difference is the technological advances, particularly as it relates to sharing information. Now, information can be passed between individuals or groups very quickly on a jobsite. When it comes to requesting information, changing contract documents and the ability to research new information, technology is extremely important.
(Q) What do you like most about working in the construction industry? How did you get your start?
The projects are always unique and bring their own challenges. The same principles in planning your work apply no matter what the situation is. I really like the opportunity to work with a team to solve problems. I started as a carpenter apprentice the summer after I graduated high school. I thought it would be like high school wood shop and was quickly surprised. The more I saw, the more I knew I belonged in construction. I was lucky to be surrounded by many talented individuals.
(Q) Talk a little bit about your experience working on historic renovations.
A couple years ago, I was part of the pre-construction team on Denny Hall at the University of Washington. We spent a lot of time up front investigating the building and applying new technologies, such as laser scanning, to uncover and record the existing details. This was one of the best management teams I’ve worked with. Watching them execute and implement Lean techniques on a daily basis with all the tradesmen was very rewarding. They measured almost everything they did. They had daily huddles to review the planned percent complete. Without this kind of attention, the modifications would have been extremely difficult due to the building’s age and history.
(Q) What takeaway can you share about Lean and green methods on the jobsite?
When it comes to Lean and LEED projects, it is important to collaborate on a plan, agree as a team and commit to the process. At BNBuilders, we have decided to focus on three categories when it comes to Lean techniques: innovation, collaborative planning and jobsite organization. Build the plan and implement the tools while measuring success as often as possible.
(Q) What is the most unique project you’ve been involved with and what made it unique?
The most unique project I have been involved with was the Seattle Children’s Research Institute. While it wasn’t the biggest project, it was one that presented some logistical challenges and took a lot of attention. Many of my team members from that project are now responsible for their own projects, from senior superintendents to senior project managers. It was a project that threaded many opportunities for others.
(Q) List a few of the tech tools you employ on the job. How do they make your life easier?
The tech tools I use the most are based on scheduling and planning. The most common tools I use are P-6 for overall scheduling, Synchro to show phase planning and Bluebeam for pdf mark-up. What really has my interest is the ability to laser scan in-house. We are only cracking the surface of what we can do with laser scanning when it comes to coordination. I see a day where scanning will be part of everything we do to document and record conditions.
(Q) What would others on your team say is your strongest attribute as a project super?
I’ve been told my experience gives me the ability to lead confidently while seeing the bigger picture. I’ve also been told I am able to assess others’ strengths, and put them in an environment they will succeed while still challenging their efforts. I truly want others to grow and succeed at what they do.
(Q) What is your advice, or the best guidance you’ve received on the job, that you can share with up-and-coming superintendents?
Some of the best advice I have received is to empower your team and remove the roadblocks. When we are in a new experience or challenge, we tend to focus on what we know the best. We can lose sight of the bigger picture and the need to provide leadership. It’s important to keep out of the weeds, but understand the detail so you can support your team.
(Q) What type of project has been the most challenging to manage? Why?
My most challenging project was one where I took the reins from someone else. This project taught me the importance of culture and a good safety program being initiated from the beginning. The hardest part was building relationships where past trust had been broken. It’s the small things you do in the beginning that set the tone for the rest of the project.
(Q) How do you establish and maintain effective and harmonious working relationships on the jobsite?
I think it’s important to listen and have a collaborative nature. Everyone deserves respect. Understanding the value of teamwork and having an open mind keeps the runway wide open.
(Q) Share a little known fact about Casey Blake that you’d like readers to know.
My family is the most important thing to me. I just became a grandpa for the first time this past May, and it’s incredible!