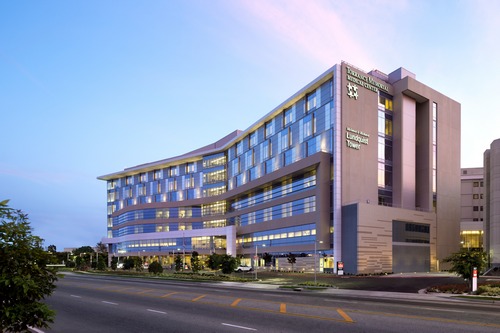
By George Vangelatos and Chuck Eyberg
Today’s project owners want reduced costs and shorter construction time, while still seeking high-quality materials. One option to explore is prefabricated exterior building envelopes. Especially when used in large projects, prefabricated envelopes are made possible by integrated teams working together to answer client objectives.
For example, take Torrance Memorial Medical Center’s Lundquist Tower in California. The expansion tower was conceived to have several skin types with elegant detailing. The project team worked together to devise an offsite prefabricated skin, which achieved high quality at a lower cost, and saved six months on the critical path of construction.
The development of the building envelope was accomplished through the “Design Assist” process, which included the architect and general contractor, as well as a structural engineer and specialty subcontractors.
The envelope consisted of two distinct systems: a precast concrete panel system and glass/metal panel system. The precast concrete panel system was used on the southern exposure and the glass/metal panel system was used on the northern exposure of the tower. The southern exposure faced inward to the campus and the precast concrete was selected to blend the façade of the tower with the adjacent buildings. The glass/metal panel system faced outward toward the community and a more contemporary “iconic” expression was desired for this exposure.
Avoiding delays with collaborative efforts
As the team was preparing the design documents for agency approval, the Design Assist team was developing their shop drawings.
The benefit of this collaborative effort is a single approval process for the building envelope in lieu of the deferred approval of the shop drawings during the construction phase. This avoided the potential schedule delay during the construction phase.
With the single approval process, the team was able to begin manufacturing the various components and assemble them into the finished panels earlier in the construction schedule.
The distinctive benefit of a panelized system, such as precast concrete panels or glass/metal panels, is that fabrication can occur offsite and the finished product stored for a predetermined installation date.
Once installation is scheduled, the panels can be delivered to the site in the sequence of installation and erected in one continuous operation.
Rolling the dice on prefab exterior, bathrooms
Another example is the newly opened 214-bed Henderson Hospital in Nevada. A combination of offsite prefabricated patient bathrooms and onsite prefabricated and assembled exterior panelized skin, adapted from the casino tower industry, was instrumental in achieving high quality at low cost, with a 27-month construction schedule.
The hospital was the first and perhaps most critical piece of the new Union Village — an integrated medical community development. As such, it was held to both the local planning department standards, as well as the conditions established by the community. These included building design characteristics, materials and application, as well as glazing and opening proportions. In addition, local climate and energy requirements played a significant role in the building skin design.
A focused team, including designers, constructors, estimators, skin specialists, structural engineers and owner’s representatives assessed several factors. First considered were types of materials.
More than 13 different skin types and wall assemblies were reviewed. They ranged from concrete panels, block walls, curtainwalls, exterior insulation and finish system, metal panels and stucco just to name a few.
Factors used to evaluate these included square-foot cost, install speed, structural impact, city and local design standards, flexibility in design, modularity, warranty, durability, skill of local labor force and LEED and energy performance.
At this point, certain wall types began to yield more advantages, yet no single wall type stood out as a paramount option.
Concurrent to the material investigations, the team was receiving preliminary planning layouts of the building. To maintain an aggressive schedule, the decisions on the exterior construction had to be made well ahead of the completion of the planning and development of final elevations. The team also relied on conceptual estimates for percentages of glazing and set targets based on a value established by both the city’s criteria and benchmarked hospitals. An 18 percent glazing target was set and assumptions made based on early planning as to how that would be distributed. This also helped to inform early energy analysis models prior to the completion of the design.
Final material selection considerations
The location, amount and distribution of glazing were not directly tied to the exterior material selection. However, it did play a significant role in the methods of assembly. For example, larger spans of glazing fared better with curtainwall systems where smaller punched windows served panelized options best.
As it stands, in the final condition there was approximately 23,764 square feet of glazing, 35,797 square feet of low-rise skin and 65,739 square feet of skin at floors two through four. With material options reviewed, the team considered the following before making any final selections:
- Should the exterior be panelized or framed in place?
- Which system will meet owner conditions of satisfaction for modularity?
- How does each system interact with one another?
- Which system(s) will allow the building to be enclosed in the shortest duration?
The team concluded that multiple options could be combined to meet the aesthetic, cost, LEED and schedule requirements and, depending on the location and desired characteristics, various options were better suited. For the low-rise or base of the building, a concrete masonry wall offered the best cost, best durability and fit well with Union Village aesthetics. This gave the design a strong and well-grounded foundation that related visually to local materials. Where large glazed areas were required, integrated glass storefront systems were integrated between the CMU walls. These areas were focused at large public spaces. To break down spans of solid wall around the building, sections of blue tile were added instead of adding more glass and cost. On the upper portions of the tower, where weight was more significant and smaller punched window openings more appropriate — an EIFS wall performed best.
In lieu of framing the walls in place, a panelized approach was used. This was a more expensive option but had significant benefits. According to KHS&H, the EIFS contractor, even though it was a few dollars more per square foot, which was going to cost approximately $200,000 more to panelize, the $300,000 saved in six weeks less of general conditions resulted in $100,000 in savings and a desirable reduction in construction duration. This eliminated the need for scaffolding and, by enclosing the structure sooner, had a significant impact on the interior finish schedule — an additional cost and time savings.
As the demand for faster, high-quality design at a lower cost continues, so does the trend toward Design-Assist, Design-Build and Integrated Project Delivery methods. With project team members working together early in the process, prefabricated skin options become possible. And that’s a trend that definitely bodes well for clients.
George Vangelatos, AIA, LEED AP BD+C, EDAC, is a principal and healthcare practice leader at HMC Architects.
Chuck Eyberg, AIA, LEED AP BD+C, is a principal at HMC Architects.