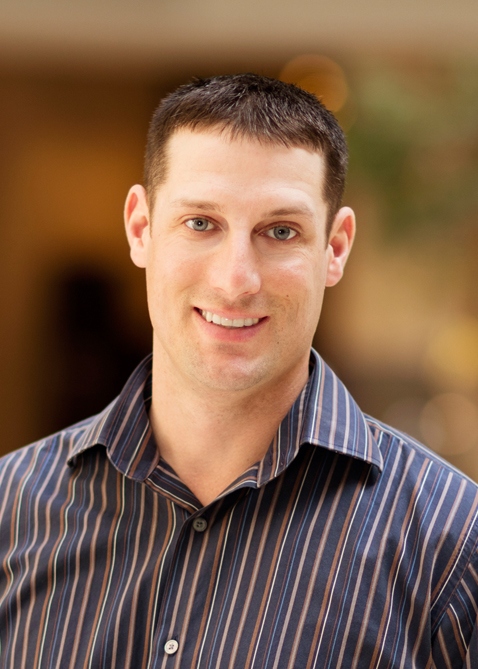
Persistence and adaptability get the job done
By Chris Maday Schmidt
With 12 years of industry experience, Project Superintendent Kevin O’Keefe has been with McCarthy Building Companies since 2006. He is the project superintendent for Erlanger Children’s Hospital Outpatient Center in Chattanooga, Tennessee, where a strong team is making a big difference. Join Construction Superintendent as O’Keefe talks about team building and buy-in, prioritizing safety, the unique challenges of constructing healthcare facilities, technology’s influence in the field and where he thinks things are headed.
(Q) Do you have a particular routine in your work day? If so, please describe it.
I get to the jobsite early and get a game plan for the day, taking a few minutes to go through any notes or outstanding items and check emails. Then, I walk the jobsite to make sure that my self-perform crews are working on the critical items and that all the subcontractors are working in the necessary areas. I check in with the foreman to see if there are any issues and make sure we are all on the same page. After, I usually head back into the office to complete paperwork and get ready for meetings. In the afternoon, I walk the job again to check production rates and see if any issues came up during the day. I try to spend as much time onsite as possible to be available for subcontractors. This ensures we are answering questions and providing information as quickly as we can to stay on schedule.
(Q) What type of safety training do you employ with field personnel?
Safety is the most important thing that we do every day. Every person who comes on our jobsite is required to go through a safety orientation. We conduct all-hands safety meetings and stand-downs where we will pick a topic to discuss with all tradesmen working on the jobsite. We also do weekly “Toolbox Talks” for the McCarthy tradesmen on the jobsite. However, the most impactful thing we do is work with team members individually as issues arise. One-on-one time ensures each worker understands everything covered in the orientation/safety meetings.
All new hires go through a new employee training program with their foreman. The NET program covers in more detail the safety precautions for their job responsibilities. We also use a task hazard analysis program that requires tradesmen to think about the job that they will be doing that day. This provides the opportunity to have a conversation with the crew, discussing how to safely complete their task and identifying any safety issues that will need to be overcome or eliminated. A new THA must be filled out each time the crew changes tasks. This process is instrumental in supporting our safety culture onsite.
(Q) How do you engage team buy-in from your subcontractors as far as safety and quality control?
Buy-in can be one of the most challenging things, especially in smaller markets where the local safety culture is not up to the standard we typically see in larger markets. Mandatory orientation sets the tone for the project from day one. After that, it comes down to enforcement. When trades know safety policies will be enforced, and understand how certain procedures protect them, they are typically on board. Issues arise when the only mention of safety is at orientation. People tend to default to the normal means of operation without a continual safety focus.
(Q) What has been the most memorable project you’ve overseen? What makes it stand out?
The most memorable has probably been the Erlanger Children’s Hospital Outpatient Center. It is not the largest project or the most challenging of my career, but we have a very strong team that has made the project really fun. While there are people on the job from the McCarthy team, the Erlanger team, the HKS design team and subcontractors, we work together as a unified team. We all previously worked together on a very challenging project before CHOC, which built a strong foundation of trust. The project runs very smoothly because of our cohesive team.
This has also been my first children’s hospital project, and the excitement and involvement in the community is very fun to see. We have had several interesting items donated to the hospital to make it a unique environment, including a tow truck, fire truck and steam engine. We had to work with the donors to make sure they were ready when needed in the construction process, and determine how to get them to the site and into place within the building. This project has other interactive elements, like a secret garden and murals painted on the wall by a local artist. To sum it up, this project was just FUN.
(Q) Can you speak to some of the unique challenges of constructing military and/or healthcare facilities?
The two main challenges in building healthcare facilities are coordination and meeting code/design requirements. The standard building systems in healthcare are more robust and must be coordinated with additional systems like medical gases, nurse call, infant protection and patient-monitoring systems, to name a few. All of this makes the overhead coordination of the utmost importance and very challenging. Additionally, each room is designed for a very specific purpose, making in-wall coordination much more critical. Things like receptacle locations and med-gas outlet locations have a huge impact on the overall functionality of the spaces. In some instances, a few inches can make all the difference.
The second challenge is keeping up with all codes/design requirements. In a healthcare facility, each department has its own codes/design requirements that you need to know and understand. Codes change frequently as new research and technology is implemented. Construction teams need to keep regulations in mind and be prepared for inspections and the potential for new requirements introduced throughout the project.
(Q) How are you seeing technology’s influence in the field? Where do you think things are headed?
Technology in the field is constantly changing and improving. In my 12-year career, I have seen the death of the fax machine and rubber stamps, the implementation of smartphones and electronic drawings, while 3D coordination is becoming standard practice. Submittals, RFIs, contract drawings and 3D models are now always at your fingertips. This easy access to information has made the field much more efficient. Our new challenge is keeping this information well organized and maintaining easy access.
We are headed toward the day when paper drawings are non-existent. The use of 3D modeling will continue to improve, and augmented reality will become one of the technologies used to inspect and coordinate projects. We also will see more projects strive to become net zero for power and water. In the field, we may see extension cords go away as more tools become battery operated, and tool tracking systems will become more widely used, hopefully eliminating lost/stolen equipment.
(Q) What would you say are the most important qualities of a superintendent?
Persistence and adaptability are key. Persistence is required to get anything done. It will not all happen easily. You will have to continue to push to get information, production, progress, anything really. You must know what results you want to achieve and then be persistent in pushing the project and team to make sure you get there. Adaptability is necessary because the best laid plans never work out as expected. The best superintendents plan for changing circumstances. They know how they want to get any task accomplished but also have two or three backup plans so they can quickly shift gears when needed.
(Q) Share the best advice you’ve received in your career.
The best advice that I have received is to be open to opportunities. Often, our careers take us to new cities, new projects or new roles and you grow from taking on those challenges. I have relocated a few times for projects and wasn’t always excited for the move. However, each ended up being great experiences for me and shaped my career. This also applies to taking on different roles and responsibilities. You may be asked to manage a project type outside your expertise or take on new responsibilities. These are opportunities to learn and grow.
(Q) Have you experienced the effects of the skilled worker shortage and, if yes, how is McCarthy Building Companies Inc. combating it?
Yes, there is a shortage, especially when they are non-union, although we don’t feel it as much with subcontractors as with self-perform markets. In the Southeast, we still get a lot of MEP contractors who are unionized. One area where unions are doing well is with the training and apprenticeship programs. Unfortunately, there are a lot of trades in the Southeast who are typically non-union and untrained. I experienced this trying to hire teams for our self-perform work, whether concrete form carpenters, finish carpenters or door and hardware specialists; it is hard to find qualified people.
At McCarthy, we are working to develop a trades training curriculum and have pulled experienced superintendents and carpenters out of the field to dedicate time to training new hires. They are currently going jobsite to jobsite training new hires with basic safety and carpentry skills.
McCarthy is also focused on building the pipeline of future employees. Part of the problem is there are not enough young people coming into the market to replace craft professionals aging out of the workforce. McCarthy supports programs like The Construction Education Foundation of Georgia and SkillsUSA, a national nonprofit student organization that promotes a skilled workforce through mentorship. We also work with local middle and high schools to introduce students to the variety of great job opportunities in construction.
(Q) Talk about a recent challenge on the job and how you overcame it.
One of the unique challenges of the Erlanger CHOC project was coordinating and lifting donated items, including a restored 1950’s tow truck, a fire engine cab and an 1891 steam engine and tinder that will serve as interactive elements on each hospital floor. None of this was really in our scope of work as all these huge items were donated after the drawings were issued. Through intense coordination with service providers, including B&B Crane in Chattanooga and the local ironworkers’ union that provided riggers, we got everyone on the same page and successfully got the job done. The unity of our team and the generosity of the community made it possible.
(Q) What would your ideal construction project look like?
My ideal project would probably be another children’s hospital. They are unique experiences that everybody is excited for. That project would be on a site with lots of room for laydown. Money would not be an issue, not that there would be an open checkbook but just that if the owner wanted to do something it would just be done. A lot of times an idea comes up and we go through cost studies before it changes or we wait until the end of the project to see if any money is left to add it. I would just like for the owner to be able to say, “That’s a great idea; let’s do it.” The other key component to the ideal project is the entire project team. Everybody would be engaged, high-performing individuals working in unison toward the same goal. There would be open collaboration and a one-team mentality, similar to the Erlanger CHOC project team.
(Q) What is your favorite pastime?
I love to spend time with my family. My wife Sarah and I have a one-year-old daughter who amazes us, and I like to be there to see her grow, change and learn. It’s amazing how fast that happens. Other than that, I golf as much as possible. I enjoy shooting sporting clays. And I am usually training for a triathlon or run. The hard part is trying to balance all of it.