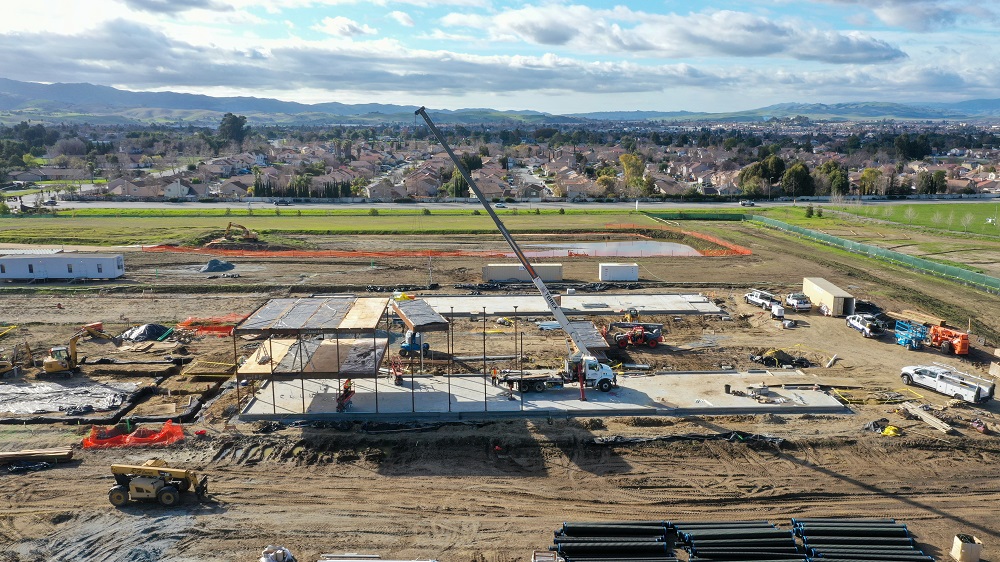
How modular classrooms help with COVID restrictions, supply chain challenges + dwindling workforce
By Robert Ussery
It’s no longer your father’s classroom… or even yours, for that matter!
Modular construction has come a long way in the past few decades. What was once little more than a construction system for quickly building portable classrooms, has evolved into an efficient and cost-effective way to build aesthetically pleasing schools.
As a case in point, Otto Construction – a 75-year-old family business based in Sacramento, California – recently completed work on the Rancho Santana School in Hollister, California, about 90 miles south of San Francisco. The school features three buildings with 35 classrooms and an administration/library building and serves 850 students.
The two-story complex was delivered by a Design-Build partnership of Otto, JL Modular and NMR Architects, and the structure was completed in 17 months. Compare that to a standard school site that would have taken 24-26 months to complete. This accelerated construction time is one of the main benefits of using modular construction, along with the fact that schedules are more predictable since we know when the modulars will be delivered and are confident they will ready to be placed when they arrive.
The Rancho Santana project utilized steel-framed structures prefabricated and inspected in a factory while site preparation was occurring. JL Modular uses a standard structural system, and workers are skilled in assembling the frames, flooring and ceilings since sizes are standardized. Now, however, the modulars can be built in a range of standard dimensions – length, width and height – which gives the architect more flexibility in design. Because both sitework and modular construction were taking place simultaneously, by the time the ground was ready, we were able to immediately begin trucking the modulars in and quickly assembling them into place.
Another huge advantage of using modular construction in building schools is that the modular contractor already has needed signoffs from the Division of the State Architect, which provides design and construction oversight for K-12 schools, community colleges and various other state owned and leased facilities. All school plans must be approved by DSA before construction begins to ensure they comply with code requirements. With an individually designed site-built project, that process can be lengthy, but since modulars have been reviewed and approved by DSA already (through pre-check, or PC, approval), we can bypass most of those reviews. That also saves time and, ultimately, it saves money for clients.
We have been able to continue to work through the pandemic because of the predictability of the materials associated with any modular construction build.
We’ve also found there are other potential advantages to using modular. One is labor – you need fewer workers onsite, and the offsite modular construction labor costs can be lower. Another is noise abatement. Since nailing takes place mainly in the factory, the jobsite is just a lot less noisy, which can be an advantage when you’re building on an existing school site or near homes.
And especially important now, with all the constraints in the supply chain and the skyrocketing costs we’re all seeing in construction, it is also helpful to buy a lot of the materials early in the process so you can at least hope the price is more guaranteed.
Otto has been utilizing modular construction in some of our school projects for years. It’s been a great way to get classrooms built quickly, particularly if the work needs to be started and completed during summer vacation. With these three-month summer projects, we can jump right in when school is out and complete the work before the next school year begins in the fall.
In all, we’ve worked on about 20 projects during the past five or six years where we’ve used some sort of modular construction. Deciding whether to go that route or to stick with site building depends on what the client wants. There are some design features that modular can’t provide, so in order to maintain a client-centric approach, we always work to establish the needs of the client up front and then compare the costs of utilizing different construction techniques and their strengths and weaknesses before determining the best approach.
All the modular projects we’ve been involved with have been for schools. I know some contractors have tried using modular for hospital projects, but there’s a strict testing and approval process in California for hospitals since the Sylmar earthquake back in 1972. It can prove challenging to receive approval from the state.
We’ve also looked at using it for some office projects we’ve been involved with, but we haven’t been able to make it pencil out. I really do believe, though, that the use of modular construction and other prefabbed installations will continue to grow. For example, schools have communal bathrooms that have as many as 30 urinals. Normally, installing the plumbing and fixtures would take a couple of weeks, but now we are able to just bolt the plumbing down in advance and then build walls around it. That kind of time- and cost-saving method is going to continue to grow in commercial construction.
Finally, from a contractor’s perspective, it’s been especially gratifying that many of the projects Otto has been working on include continuing technical education classrooms. Here in California, school districts focused for many years almost exclusively on the college-bound track, which is one reason our industry is facing such a labor shortage these days – up to 20-30% in some trades. But the sentiment about CTE has shifted. We recently completed work on a large CTE building for King City High School, 60 miles south of Hollister, and we are now working on an innovative culinary arts pathway facility at a high school in the Sacramento area. It’s really cool to see these programs returning, and for being a part of making it happen.
It’s like my dad always told me – if you can work with your hands, you’ll never go hungry.
Videos following progress:
January 2020: https://youtu.be/WtCgpehQAQQ
June 2020: https://youtu.be/Q5Sr_LR0pOo
November 2020: https://youtu.be/qRaA-x-edQg
January 2021: https://youtu.be/5RHeIGmzgtw
Robert Ussery, DBIA, CM-LEAN, is general superintendent at Otto Construction.