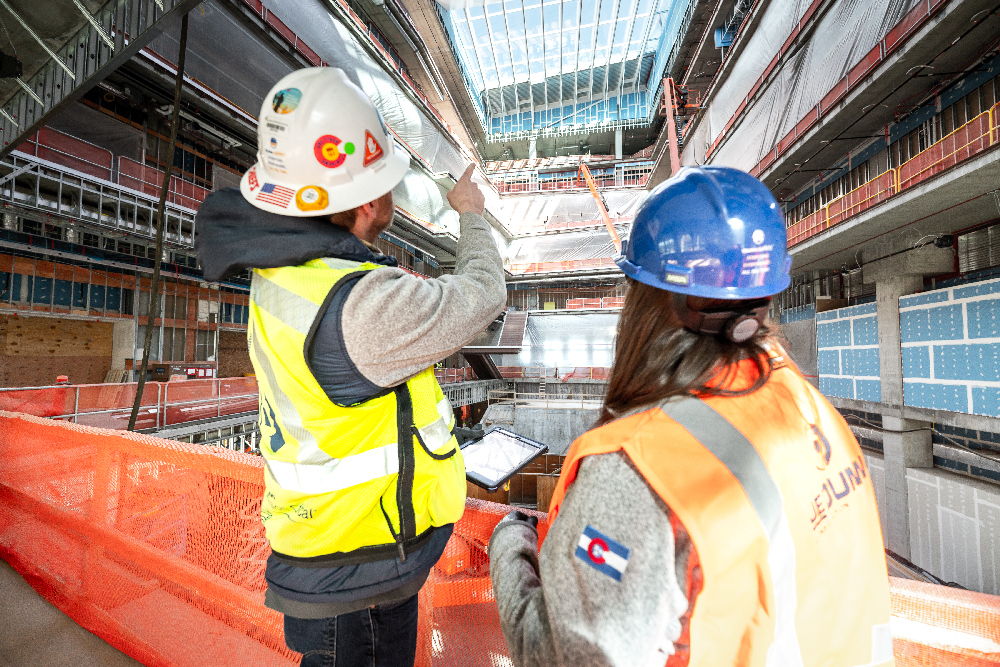
A Superintendent’s Approach to New Technology
By Devin McLaren
Technology is constantly evolving to not only change the way we build, but also to change the way project teams collaborate and problem solve in a challenging landscape. To achieve such progress, technology and innovation must play a key role in offering craftsmen and women new ways to improve means and methods, efficiency, speed-to-market delivery, safety and quality control.
Technology is critical to construction both in the design and in the building process — the advances that have been made over the last 20 years save time and money every day — and the advancements in safety have taken that to another level, as well. In short, technology is the real reason that we can build bigger, better and faster buildings than we could five years ago, and there are some best practices in implementing technology that increase efficiency and play an integral role in project success.
Make sure it’s practical
While new technology is exciting, and there are many options out there, make sure it works for the team. Technology just for technology’s sake doesn’t do any good unless it directly meets the needs of the project and creates efficiencies for the team. If we deploy technology every time something new and cool comes along, it can actually have the opposite effect, taking the team away from daily tasks to learn the system in addition to the learning curve of the processes affected by the change. Just because it is new doesn’t mean it has any benefit; make sure the team and those using the new tech thoroughly vet it prior to rolling it out. At the end of the day, technology must bring the owner and the team value in safety, quality, schedule, budget, production, etc.
Train the team
Just as technology needs to be practical, it can only enhance the construction process if the users implement it correctly to maximize its impact. While project teams are trained as technology is initially rolled out, it’s important to communicate with each other as people start to discover the ins and outs of what it has to offer. As people use new tech, they are sure to find shortcuts or capabilities within the programs as they become more familiar with it, so passing along tips or things they’ve learned only benefits the entire team and further compounds the technology’s effect on the overall project.
Stay selective
With new technology being introduced all the time, it’s important to resist getting caught up in the flashy sell; make sure it’s a good, useful tool and is a benefit for the team as a whole, as well as clients. “This should go without saying, but technology needs to simplify the day-to-day items for the team, not complicate them,” said General Superintendent Jason Pruitt. “It should help minimize or eliminate tasks, not make more work. Tech has improved so much of our lives — and at such a rapid pace — that sometimes we fall into the trap of finding the next great thing. That’s why it’s so important to stay selective when making changes or rolling out upgrades.”
Apply it universally
Practicality and selectivity are important, but equally important are access and usability for the entire team to truly maximize efficiency. This includes both jobsite tech and processes for tools sourcing to keep projects running smoothly. One of the biggest challenges faced on jobsites is management of construction documents such as drawings and checklists. To streamline the process and alleviate the issues outdated documents may cause, JE Dunn recently deployed CMiC mobile for all new projects, equipping project teams with iPads loaded with the software — and that includes trade partners. “As part of a company initiative to identify areas where we could become more efficient, CMiC was identified as the primary tool we need to be successful for construction document management, said Operations Technology Director Patrick Miller. “In addition, we were able to make it accessible for all trade partners, which was key to maximizing the impact technology can have on each project.”
To build on universal access for jobsite tech, the Blue Hat and Procurement organizations at JE Dunn will be deploying a new and improved e-commerce system designed with the field operator in mind. This new platform will provide a modern and mobile accessible catalog of inventory and rental items available across the Blue Hat network of warehouses and facilities. “In these economic times, our ability to transact business not only faster, but also more efficiently, is paramount to project success in every market. Deployment of this system in October is just one of several steps we are taking to streamline our overall supply chain,” said Procurement Director Jason Banks.
Lasting impacts
Technology is also contributing to a key factor in project success — speed to market. The advancements in BIM and the way teams collaborate with each other and with clients directly impact cost and schedule. “BIM captures and fixes issues prior to material fabrication, so the time saved identifying and correcting these potential problems on the front end can save substantial time,” said Pruitt. “At the end of the day, speed to market is critical to every client. Advancements in technology have enabled us to deliver quicker at a time clients need it most.”
Advancements in field technology have greatly impacted the way we build — particularly in recent years — but there is one advancement that is having a larger impact that trickles down to many aspects of the job, and that’s in the layout industry. GPS advances and GPS installed in trucks allow you to know exactly where you are onsite and what elevation grade is at; GPS installed on earthwork equipment takes out the people mistakes and the need for staking sites multiple times; Dusty Bot (robot on wheels) replaces two people and can handle double the production with layout.
So, ultimately, the lasting impact of technology is that we can now do more with less people and do it accurately and efficiently. This helps alleviate the challenges of today’s labor shortage, while also increasing safety and quality.
Devin McLaren is general superintendent at JE Dunn Construction.